Rolling Railway Maintenance to a Digital Destination
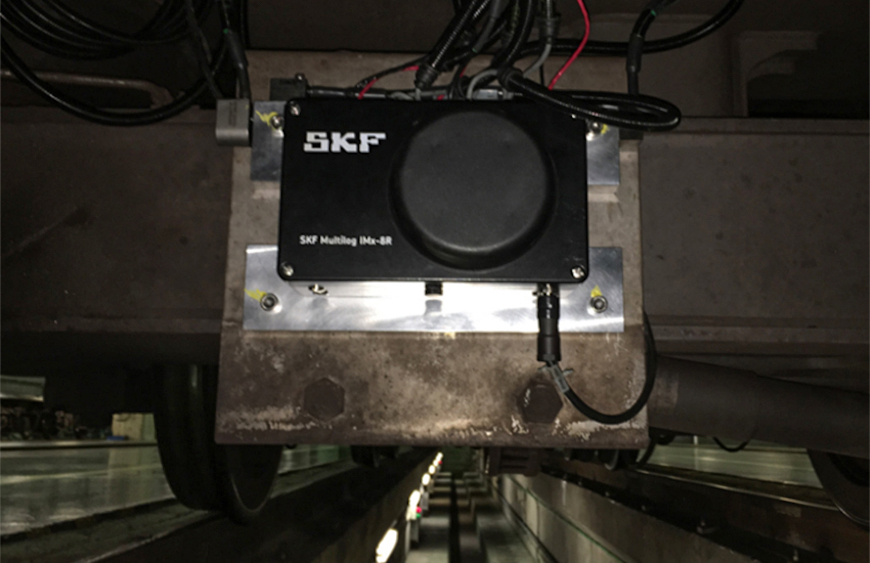
In the rail industry time is valuable currency. SKF’s latest digital innovation is proven to extend maintenance levels and keep rolling stock rolling as much as possible.
Condition-based maintenance (CBM), which involves measuring and monitoring parameters such as vibration and temperature to spot anomalies at an early stage, has been applied for a long time in many industries. The monitoring aspect is commonly known as conditioning monitoring.
Historically, the rail industry’s maintenance regime is to service trains on a time or mileage basis. Though this approach has been used successfully for many years, it does not take account of whether parts actually need replacing. Inspection can only take place when trains aren’t running, and maintenance actions require rolling stock to be taken out of service, or lines to be closed for extended periods.
As such, maintenance costs remain one of the biggest concerns for the industry, due to aging train fleets and the increasing need for train availability.
Adoption of CBM is steadily growing thanks to significant innovations and the availability of technology. Digitalisation is making a major difference towards how maintenance is executed and can enable the customer to extend maintenance intervals. This can have beneficial effects on, for example, train availability. The less time rolling stock spends in maintenance, the more time it can spend carrying passengers or cargo – this is important at a time when the sector is seeing increased pressures on demand. It can also help with reducing life-cycle costs and inventory management of spare parts, due to the early warnings provided by condition monitoring of any risks and possibilities of incidents.
SKF has combined CBM with its knowledge in bearings and other components and developed an entirely rail-focused version of its highly successful Multilog IMx platform. This latest innovation combines rolling stock and track condition monitoring in a single, easily customised solution.
The Next Step in Train Digitalisation
Multilog IMx-Rail is a multi-channel, on-line condition monitoring system based on new rail-approved components. It is the next step in train digitalisation, allowing operators to implement condition-based maintenance that can help achieve goals such as TCO reduction, higher availability, the avoidance of unplanned stoppages and longer maintenance intervals.
Available for OEM installation and as a retrofit solution, Multilog IMx-Rail offers advance warning of rolling stock rotating part issues on wheel bearings, gearboxes and motors, as well as data collection from many other components. The system can also provide a track health-map with line faults located, identified and recorded with market-leading accuracy.
The Multilog IMx-Rail system can also be integrated easily with SKF’s cloud services for data storage, data sharing and for SKF Remote Diagnostic Services. Its versatility, combined with SKF’s expertise at monitoring rotating components across many industries, enables the quick analysis and prioritisation of any planned rolling stock maintenance.
Proven on the Tracks
Multilog IMx-Rail is already demonstrating its capabilities in the field. To provide a sense of how the system typically works, on a standard commercial train, for example, the self-contained package of sensors and electronics is mounted on to one of the train’s bogies, under a carriage. In everyday operation, the unit measures and records acceleration and vibration signals, it then processes this data and transmits all the information wirelessly to a back-office collection point, where reported information can trigger required actions.
Next, a dedicated software system, also provided by SKF, uses smart algorithms to analyse the sensor’s data, along with information on the train’s location and operating conditions. The software system, called “@ptitude Observer”, identifies, locates and accurately records rail track abnormalities that might generate wear or damage to the train’s wheels, cause passenger discomfort, or result in noise on particular parts of the track.
Maintenance staff can then use that information to trigger a more detailed inspection of the area of track identified.
Multilog IMx-Rail doesn’t only help operators understand the condition of wheels and track. The system is also designed to identify vibrations caused by other problems on the train, such as faulty bearings. Operators around the world are already using this approach to avoid breakdowns and optimise their rolling stock maintenance schedules.
As rail traffic increases, the role of digitalisation and condition-monitoring solutions, such as Multilog IMx-Rail, will become increasingly more important in boosting rolling stock efficiency and keeping trains on track.