Rail Maintenance: Defining the World’s Gold Standard
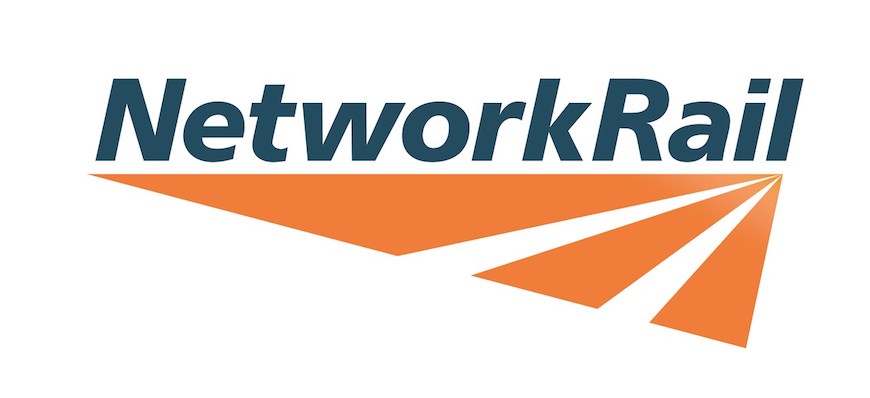
Here’s a problem that railway operators around the world are all too familiar with: how to manage thousands (often tens of thousands) of miles of track and an almost impossible number of stations, platforms, signals, bridges, tunnels, crossings, cuttings, embankments and viaducts, keeping everything maintained in optimum working condition.
When equipment fails, delays are inevitable. And not just to one train, on one journey, but to the many passenger and freight trains scheduled to follow. Of course, proper inspection and carefully scheduled maintenance helps to minimise equipment failure but that’s tough to manage when you have assets numbering in their tens of thousands.
Unfortunately, faults aren’t always easy to diagnose and they can be impossible to predict. Perhaps there’s an undetected manufacturing defect. Or even a series of minor failures that combine to create a single catastrophic event. In the best case, there will be a delay while the problem is fixed – tempers rise, refunds are paid and reputations get damaged. And the worst-case scenario? Well, everyone’s nightmare.
Making Railways Work
According to David Tickem, Thales’s Technical Manager of Integrated Communication and Supervision Systems, even the best maintenance doesn’t come with any guarantees. “Maintenance will never completely eliminate equipment failure. Anything with moving parts has the potential to fail,” he said. “Points are a good example. We all know that they’re used to move trains from one track to another and, as you’d expect, they rely on well-greased bearings. But rain washes grease away. Less grease means more friction and more friction means more work for the motor.”
Clearly, extra stress increases the chance of equipment failure. But no railway can afford to strip down, inspect and reassemble tens or even hundreds of thousands of assets with sufficient frequency to totally eliminate the possibility of failure.
Not only is maintenance expensive but, in itself it can be the cause of delays. Plus, of course, you’re sending engineers into dangerous environments.
That’s why Predict and Prevent, which is being pioneered by Network Rail in partnership with Thales, is causing such a stir around the world.
Continuous Monitoring for Maximum Efficiency
“Predict and Prevent starts with monitoring,” explains Tickem. “By attaching cable clamps to current-bearing cables, for example, we can measure how much current is being drawn. If we can see that whatever we’re monitoring is drawing more current than usual – if its working harder than normal – then the issue is flagged for investigation.”
This non-invasive monitoring is a major attraction of Predict and Prevent. Nothing has to be examined and nothing needs to be taken apart, but the operator benefits from accurate, real-time information about the status of each and every connected asset, which means that engineers can be deployed before anything fails.
Importantly, Predict and Prevent also lets rail operators deploy their engineers more effectively. The early warning it provides means that maintenance can be carried out not only as soon as it is needed, but also at the most convenient time – when it won’t interrupt train services, for example.
Predict and Prevent is capable of reporting thousands of incidents a day but, for the sake of simplicity, let’s assume that it has detected that a non-essential component will fail in 30 minutes; that a crucial component could fail within a few hours, and that an embankment has shifted after torrential rainfall, presenting the possibility of a landslide.
Nothing has failed yet but you can see what will, when, and how important it is. That’s the sort of information that’s invaluable when you’re judging priorities and deciding your action plan. That’s the sort of information that optimises engineering efficiency, reduces delays and improves safety.
The Future of Rail Efficiency
Now that the concept of Predict and Prevent has been proved (Thales is already helping Network Rail to continually monitor more than 42,000 assets in the UK), Thales is in active discussions with rail networks around the world. At the InnoTrans 2016 event in Berlin, enquiries flooded in from Australia, USA, China and from countries too many to mention across Europe and Asia-Pacific.
“Predict and Prevent is eminently versatile, scalable and exportable,” commented Tickem. “Regardless of the assets you want reports on, or the data you want and how you want to use it, this is a truly universal solution for rail transport asset management and maintenance. What’s more, we can supply it as a complete end-to-end service, letting rail companies focus on the core business of moving people and freight.”
“Once the service is up and running we can monitor pretty much anything that the customer wants us to. The track, points, point heaters, power supplies, cabling, temperature, hydraulic fluid levels, voltages, high frequency noise, embankment stability, everything.”
Managing and Analysing Data
Real-time data is reported into the customer’s system, and Predict and Prevent will flag problems as and when they occur. At this point they can use the system for further investigation and determine the correct course of action.
It’s not just a question of reacting to alarms, either. Predict and Prevent can detect whether the asset is degrading rapidly or slowly and it can report its recent and longer history. The next evolution is to leverage cloud computing and ‘Big Data’.
“We are working with customers to use their data to identify the patterns and trends which would otherwise remain undiscovered, said Tickem. “We are developing methods of understanding how their assets behave, when they are likely to fail and how to reduce the impact of that. This is a big step forward. This is the gold standard of rail maintenance.”