Position Sensing of Mechanical Components in Rail Increases Safety
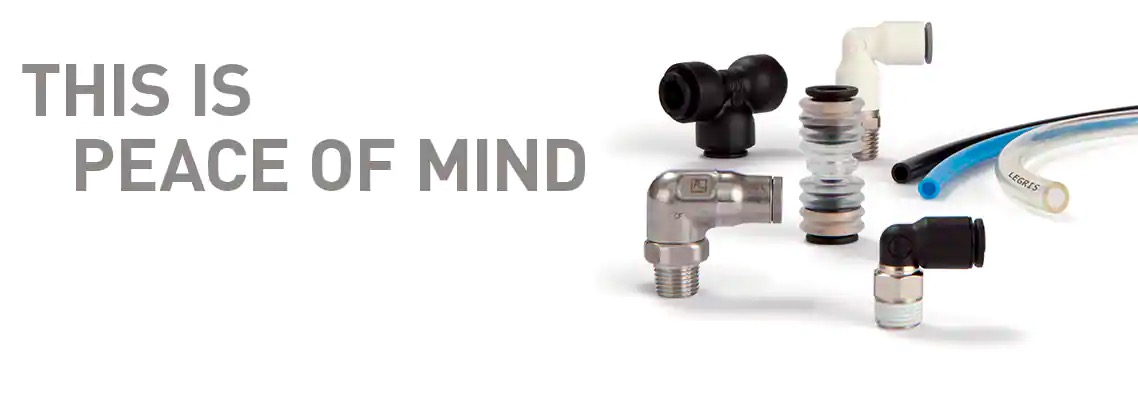
Whether train driving is done manually or automatically, human being remains responsible for safety. Man is increasingly assisted by automatic means to control and communicate with his machine. This assistance is provided by systems called Human Machine Interfaces (HMI).
The objective of the HMI is to make the facilities more functional, better adapted to the environment and to avoid risks. For this reason, electronic systems are growing to benefit passenger and goods safety but also for the productivity of equipment.
In trains, the HMI are deployed on different mechanical components in the form of electronic systems. They can be placed on the mechanical components of a pressure circuit to monitor and control their operation.
How Do HMI Optimize the Operation of Railway Mechanical Components?
The sensor is an element of the HMI more and more used in the architecture of mechanical systems of a train, especially in pressure circuits. The assembly of sensors on mechanical components allows precise control of movement in pressurized fluid transfer systems, thus improving safety.
These sensors are detection devices with signals that make it possible to bring intelligence to the control of the movement. They provide the
data needed to foster a reactive and preventative environment. Position sensors, for example, make it easy to control the open or closed position of a valve on a fluid transfer circuit.
The use of a sensor with electrical or contactless technology minimizes the overall cost of implementing a secure mechanical system. Indeed, it allows to quickly and accurately detect the open or closed position of a circuit, without separate encoders and especially without additional mechanics.
The data transmitted by the sensor allows the monitoring and, when the information flows in both directions, the control of the mechanical component itself. Position data available improve risk control and prevention by quickly detecting any problem and saving it to databases. The HMI then makes it possible to avoid malfunctions that can lead to downtime or productivity losses.
Parker Legris Valves for Railway Applications
Several fluids are circulating in a train between a tank and actuators such as brake shoes and motors. The medium conveyed range from compressed air, water or glycol water, to diesel or hydraulic oil. Some circuits need to be secured.
Well known for its expertise in fluid transfer solution, Parker Legris has developed a new lockable valve with sensor, adapted to the low-pressure circuit for compressed air supply. Thanks to this valve with open or closed position detection, the user quickly identifies the valve status and can act faster at the exact location.
The new Parker Legris valves have two additional functions:
Locking the lever via a lockable plate to prevent unintentional manipulation.
Detection of the open or closed position state of the valve via a position sensor. This sensor will directly transmit the information to the driver in the cabin or to other electromechanical devices of the circuit to modify their operation if necessary.
To adapt to the railway equipment constraints, the new valves have a robust IP67 protection box at the sensor. They are 100 percent leak-tested and have an inductive sensor electrically connected to the HMI.
Electronic sensors are now essential safety instruments in railway vehicles. They are expected to expand to more mechanical components, because safety is at the heart of the innovation of railway market players, and more widely of manufacturers like Parker.