Fraunhofer Conduct Research on Noise Emissions in Rail
Noise Emissions in Rail Vehicles
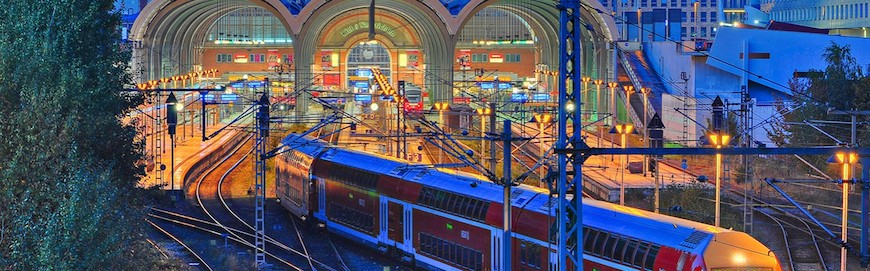
Environmental noise has a huge impact on people’s health and quality of life. Industry and the transportation sector play a significant role in noise emissions, especially in urban areas. As a result pressure on transport vehicles (road, rail, water etc.) to manage their noise output is increasing all the time. This means that all transport vehicle components that contribute to overall sound radiation must be acoustically optimised. One of the major noise sources in rail vehicles is the drive train, consisting of electrical drive and transmission. The noise emissions of these components usually have a significant tonal character with certain single frequencies that make them both prominent and annoying.
Acoustic Optimisation of Rail Vehicle Components
Researchers at Fraunhofer Institute for Machine Tools and Forming Technology IWU, Dresden conducted a project to develop a simulation-based method to optimise the acoustic behaviour of gear transmissions, which was evaluated on a single stage spur gearbox of a railway vehicle. A dynamic simulation model was used to identify acoustically critical operating points at a defined input torque and to find optimisation potentials to reduce noise emission and to shift acoustic phenomena out of critical speed ranges. To reduce the overall sound radiation of the gearbox in critical speed ranges, two acoustic optimisation solutions were performed in parallel:
-optimising the gear micro-geometry
-structurally optimising the gearbox housing
A significant overall reduction of the sound radiation can be achieved by lowering the excitation potential of the gear mesh; this is done by changing the micro-geometry of the gears. Using a parameter study (DoE), the optimal gear geometry parameters were determined; reducing the first gear mesh order was made a target parameter, while the load capacity of the gears was also considered for reasons of durability. Optimising the construction of the gearbox housing within the given installation space and weight limits changed the dynamic system characteristics and reduced the system’s sound radiation. The radiation characteristic of the gearbox can only be influenced by optimising the housing, which is done by shifting relevant operational deflection shapes in the frequency domain caused by mass and stiffness changes.
The Research Results
The results show the highest potential for noise reduction in lowering the dynamic excitation of the gear mesh by optimising the micro-geometry. The sound power level can be significantly reduced by approx. 8dB if micro-geometry and housing modifications are combined. Optimising the structural properties of the gearbox housing alone lowered the overall sound radiation by approx. 2dB. This is based on the fact that the radiation characteristics of the structure cannot be completely changed by modifying mass and stiffness, given the design restrictions. Additionally, the relevant operational deflection shapes can be shifted to frequency ranges which are less critical from an acoustic point of view.
The presented simulation approach can be applied to different types of gearboxes and is an important tool for the acoustic development of gearboxes, especially in the early design phase.