Large Cable Railway Requires Special Damping Solution
The dampened drive-in of two exceptionally large cable railway supply cars into the stations required the designing and installation of special damping solutions.
www.ace-ace.com
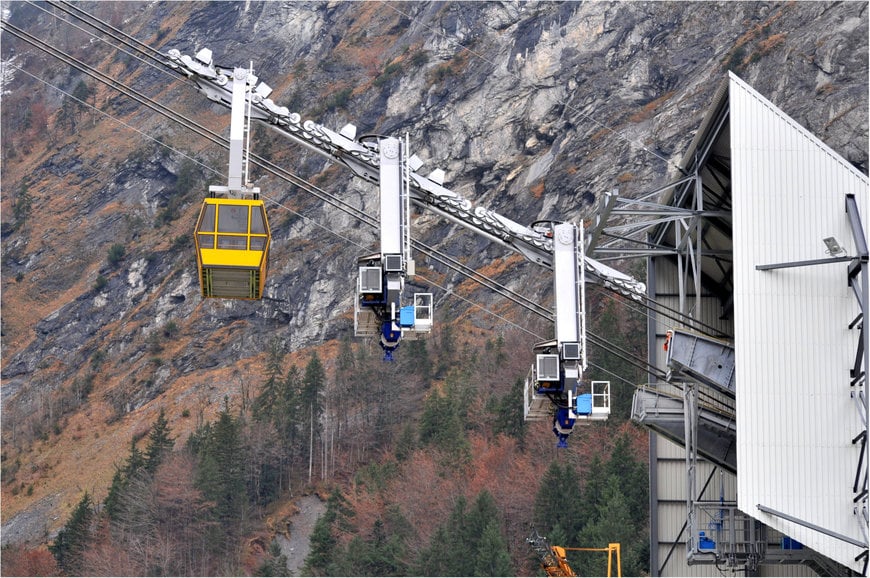
With a payload of 40 tons, moving cable cars must be fast and reliable but also be braked gently when driving into the valley station. To manage this task it was necessary to develop novel internal shock absorber sleeves and adapt them to fit heavy industrial shock absorbers. BIBUS AG in Switzerland and German ACE Stoßdämpfer GmbH solved this case for their customer.
90 mm thick support cables with a weight of almost 50 kg per meter, three phase motors with 1,150 kW rated power, a payload of 40 tons and this times two. All this to ensure the supplying of an underground hydroelectric storage power plant during its enlargement, two supply cable cars were made, which may be called the largest in the world. To ensure that these vehicles slow down safely on entering the station it was necessary to develop new industrial shock absorbers in XXXL size.
A Difficult Job with Superlatives
The location idyllic, the Swiss electric utility company AXPO's project formidable, that, in a nutshell is what one may call the Limmernsee dam. It is a reservoir in the Swiss Canton of Glarus that was completed in 1963, and, recently, its underground pump storage power plant had to be expanded. Since the work was completed, the pumps in the power plant are able to achieve an output of 1,000 MW. This value corresponds approximately to the output of a middle-class nuclear power plant, mind you not in terms of energy production but when considering the turbine or pump performance. At the same time, the adjoining Muttsee is the highest reservoir in Europe, a natural lake basin, being about 2,500 meters above sea level, which also has the longest dam in Europe since the works were completed there in 2015/2016.
The goal was to produce convenient base load by pumping water from the Limmernsee into nearby Muttsee. The electricity produced is sold when peak power is required. Many thousands of tons of heavy building materials, machinery and vehicles needed for the construction of the dam had to be transported across the mountain landscape. Both cable cars needed to be built according to the dimensions described because a special drill head for drilling tunnels weighs 30 tons alone. Although the surrounding is idyllic, it is very difficult to access. On this scale, accessories also require special engineering services. As during previous cable car and gondola projects, the Doppelmayr Garaventa Group, manufacturer of the giant cable car, turned to BIBUS AG, a leading Swiss manufacturer of hydraulic and pneumatic drive and control systems and equipment.
The contract was to deliver heavy industrial shock absorbers which make gentle braking of the cable cars possible when they enter the station in the valley. It was clearly evident that only a hydraulic shock absorber solution would be able to meet these requirements. These heavy machine components are not produced by the company itself but procured from its cooperation partner - ACE Stoßdämpfer GmbH in Germany. Therefore, the Swiss BIBUS product manager for shock absorbers turned to the leading supplier of systems for deceleration in Langenfeld, Germany.
An idyllic location for a gigantic project in Switzerland, where the material for building the dam at Muttsee could only be transported by cable car railways. Credit: Doppelmayr-Garaventa
Swiss Man Shouts and Sets off a Test Avalanche
It became clear after a few phone calls and emails to those responsible at BIBUS and ACE that only very heavy industrial shock absorbers would work for the case in question. ACE offers a wide range of adjustable and self-adjusting shock absorbers for this purpose. Types designated CA4x16 are self-adjusting and can brake up to 115,000 kg and when doing so accommodate up to 126,500 Nm per stroke. However, when the first damping characteristic curves were calculated with ACE's software, it turned out that the development of a new inner sleeve would be needed for the heavy industrial shock absorbers due to local requirements concerning supporting force and damping characteristics. This shows two work procedure characteristics used by ACE and BIBUS: Firstly, the end customer is always involved early and intensively in the planning process of new projects so that optimum results are obtained.
Secondly, if requested, the damping specialists can deliver more performance by providing special models as mentioned here. To decelerate the 48,355 kg heavy total mass and the energy absorption of 99,000 Nm per stroke would be a task difficult to accomplish even for the normal CA shock absorber series, but when does a shock absorber normally have to stop a cable car of this size? For comparison: The supply railway in Switzerland is equivalent to a passenger train that could accommodate approximately 500 people. In this case, the incredibly high energy-uptake is derived not only from the weight of the braking mass but also from the fact that the special CA4x16-S-2955 industrial shock absorbers finally used must fulfill two distinct functions: The first is braking during normal operation. Secondly, it is also responsible for a safe stop in case of an emergency. And, if the situation arises, it must also be able to dissipate more kinetic energy than in "normal" circumstances because if failure occurs, the approach velocity is 1.0 m/s, which is two and a half times that of normal operation.
This heavy industrial shock absorber is designed in a way that it can, should breakdown occur, decelerate two and a half times the speed of normal operation. While doing so, it reliably protects the end positions of the construction for an approach velocity of up to 1.0 m/s. Credit: ACE Stoßdämpfer GmbH
The dimensions of the special design are indeed identical to those of the standard production series but have a different interior and appear tiny in contrast to the huge cable cars. The CA shock absorber measures 1,300 mm in the extended state, 406 mm of which are intended for the working stroke. The previously mentioned performance data show that engineers from BIBUS and ACE are in principle already prepared for designing further record cable cars. Meanwhile, in the Swiss Canton of Glarus the work described has been carried out and the heavy industrial shock absorbers reliably did their job of converting large amounts of kinetic energy.
www.ace-ace.de