railway-international.com
24
'24
Written on Modified on
Alstom completes the first new maintenance depot in Romania designed for electric trains, in the Grivita area in Bucharest
First inter-regional Coradia Stream EMU is now at the new depot undergoing mandatory tests in view of certification.
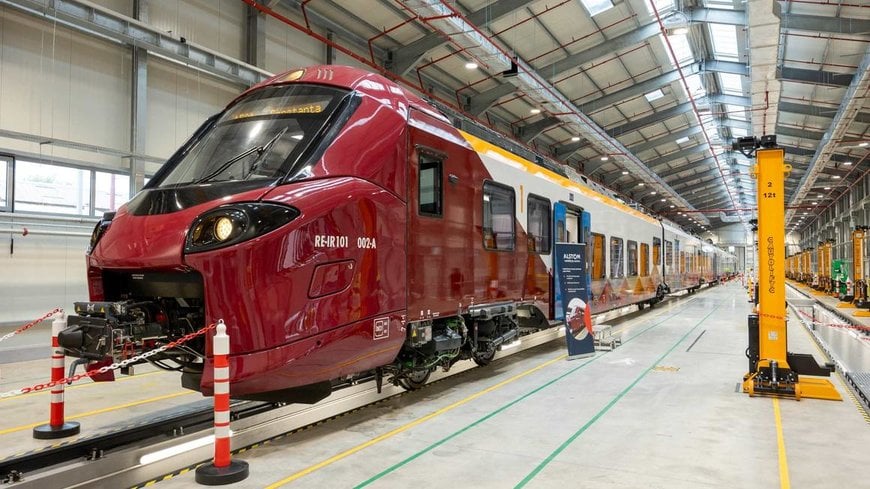
Alstom, global leader in smart and sustainable mobility, has announced the completion of a new maintenance facility in Bucharest, Romania. Alstom Grivita Depot is Romania’s first established depot dedicated to the maintenance and testing of electric trains and locomotives. Currently, the first EMU from the order of 37 units for the Authority for Railway Reform (ARF) is stationed at the new depot, undergoing mandatory testing in view of market certification.
Alstom is actively recruiting for the new maintenance centre, with approximately 50 employees expected to join the project and undergo specialised training.
“This new depot underscores Alstom’s enduring commitment to the Romanian market and marks a significant milestone as we celebrate our 30th anniversary in the country this year. Along with maintenance operations, Alstom Grivita Depot is also dedicated for testing, validation and fine-tuning operations, to ensure that the new rolling stock reaches the performances required by the contracts,” says Gabriel Stanciu, Alstom Managing Director for Romania, Bulgaria and Moldova.
“This is the first modern depot to be built in Romania in the last 30 years. The new maintenance facility will be equipped with the latest generation technology, matching, or even surpassing the most advanced depots in the world, including a digital control room for fleet management,” says Roberto Saccione, Alstom Services Managing Director for Romania, Bulgaria and Moldova.
The six-car train Coradia Stream for ARF is continuing the very complex programme of mandatory testing – static and dynamic – in accordance with TSI regulations (Technical Specifications for Interoperability) set at European level and the National Notified Technical Rules (NNTR), before being able to circulate with passengers. All the functionalities and performances of the new type of train are to be confirmed through hundreds of verification tests, ranging from electrical and electronic systems, to braking and propulsion systems, railway dynamics for the train stability, all aspects of passenger comfort and many more[1]. Following the completion of these verification tests, an additional 60 final certification tests are necessary to validate train compliance and secure authorisation for passenger operations to commence.
To optimise the process, Alstom is using three similar trains simultaneously, dividing key phases of the testing procedure. The final stage before passenger operation involves endurance tests: covering 10,000 km on commercial lines, without passengers, subject to line availability.
Alstom has been active in Romania for 30 years and is a market leader in railway electrification and signalling solutions, currently employing over 1,500 people. The company is responsible for implementing signalling or electrification solutions on the Northern branch of the Rhine-Danube railway corridor in Romania as well as on two lots of the Cluj-Oradea line as well as the first lot of the Caransebeș-Lugoj line. The company is part of the consortium building the second metro system in Romania, in the city of Cluj-Napoca, the first fully automated metro line in the country. The first CBTC urban signalling solution in the country is under implementation by Alstom on Bucharest’s metro Line 5. Alstom has also been the provider of maintenance services for the Bucharest metro fleet for the last 20 years and a new long-term contract is in place, valid until 2036.
Additional information on Testing and certification processes
The main functionalities and performances to be demonstrated according to applicable Technical Specification for Interoperability (TSI) and Notified National Technical Rules (NNTR):
Electrical and electronic systems: This includes the testing of all components related to the operation of the train's electrical and electronic systems, such as signalling, communication, train control, fire detection and passenger access doors;
Braking systems: This involves ensuring that the train's braking systems meet the prescribed standards for safety, efficiency, and performance under various conditions and over the complete train lifetime;
Railway Dynamics: This involves ensuring that the train is able to maintain stability against risk of derailment in different type of track geometry and quality and under different loads;
Propulsion systems: This testing determines the train's ability to accelerate, decelerate, and maintain speed under various conditions;
Passenger comfort: This involves assessing the passenger experience, such as interior noise levels, ride comfort, temperature control, and other features that can impact the passenger's comfort;
Crashworthiness and Structural Robustness: This evaluates the train's ability to support structural loads and the ability to resist impacts in the event of a collision and protect the passengers in the carriages;
Environmental performance: This testing is done to ensure that the train complies with environmental regulations and includes a wide range of factors such as noise pollution, energy efficiency, electromagnetic compatibility, eco design;
Train Driving Condition: This involves ensuring that driver's cabin and man-machine interfaces are safe, efficient and comfortable to ensure proper train driving;
Overall, 10,000 km of final dynamic testing without passengers, on a commercial line, is considered an adequate amount to ensure that the train meets regulatory requirements and ensure that it is safe, durable, and reliable for passenger use. This final phase is designed to ensure that the train has undergone proper validation to meet the required standards for passenger service. Testing a train for such a high distance under various conditions at high speeds helps to identify any potential defects that could develop during the train's lifetime. Additionally, it helps to ensure that any components that may wear out over time, such as wheels, brakes, or suspension, have undergone a thorough testing process and have suitable replacement plans in place.
Alstom™, Coradia™ and Coradia Stream™ are protected trademarks of the Alstom Group.
[1] Please see the extended list of the main test categories at the end of this document.
www.alstom.com