railway-international.com
01
'24
Written on Modified on
Shorter headways boost punctuality
Trains should always be able to stop safely – even in adverse conditions.
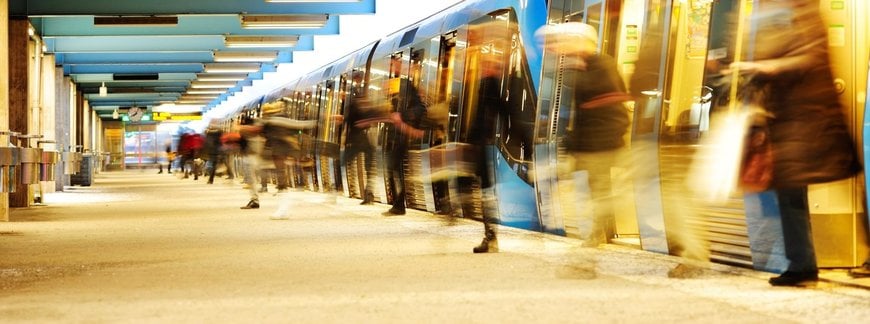
Ingenious combinations of innovative braking technologies may make it possible to eliminate currently still essential safety margins and create extra transportation capacity without having to build new infrastructure.
A defective signal, malfunctioning points, people on the track – these are just some of the reasons for train delays. Another little-known reason, however, is hidden away in the way trains actually operate. The intervals between trains are based on well-defined safety premises – every train must always be capable of coming to a safe standstill within a specified distance, even in the most unfavorable circumstances imaginable. On the one hand, environmental conditions such as wet or dry rails exert a huge influence on the length of braking distances and their variability (variance). On the other, different wheel diameters, load detection tolerances, and coefficients of friction between brake pad and disc all have an impact on the braking and stopping distances that can be achieved. Finally, the behavior of the actual braking equipment and friction pairings also changes during the braking process.
To avoid potentially dangerous situations resulting from this combination of factors, safety margins are added to vehicle braking curves and operational parameters are adjusted to suit each set of circumstances – by, for example, reducing maximum speeds in poor track conditions. While the margin or “buffer” imposes a limit on train frequency, operational restrictions can potentially result in delays. Conversely, this means that if variances in braking and stopping distances could be reduced – in other words, if they could be made consistently reproducible, even in adverse environmental conditions –, margins could be minimized and operational restrictions avoided without compromising safety. The untapped potential for improving capacity utilization is thought to be very high, especially on metro and suburban networks, as well as Asia’s dense high-speed networks.
Knorr-Bremse’s Reproducible Braking Distance (RBD) program represents a major contribution to leveraging this potential. The program is based on the functional interaction of three innovative braking technologies. First: a new type of deceleration control system (DCC). By constantly compensating – in real time – for the difference between the train’s actual deceleration and the train’s target (setpoint) deceleration, it decouples the actual deceleration from the braking system’s variable parameters while the train is braking. Second: an improved wheel slide protection system (WheelGrip adapt). The latter uses a control strategy situationally optimized for each specific set of circumstances to curtail the increase in braking distance that occurs in a wide variety of poor wheel-rail adhesion conditions. And third: a train-wide, situationally adaptive sanding and wheel/rail adhesion management system (ADM). This system regulates the train’s sand output by pre-detecting and assessing rail conditions – delivering as much sand as necessary, but as little as possible. This cuts down sand consumption and reduces the negative impact on infrastructure, while at the same time optimizing braking distances [Fig. 1].
If they were once thoroughly validated and integrated into the regulatory framework, the more reliable and reproducible deceleration values enabled by RBD could be incorporated into the braking curves and braking deceleration figures used for ATO and train control (ETCS). This would create additional capacity on existing infrastructure, which network operators could then “fill up” with extra trains or else “exploit” to reduce delays caused by disruptions. In particular, rail operations would be less dependent on environmental influences.
Fig. 1: A sanding management system with situational adaptivity regulates train-wide sand output.
Current development status
First launched in 2018, the development of the various RBD functions is now well advanced. The first step was to quantify the decrease in braking distance variance in DCC mode on a test track. During service braking maneuvers at a speed of 120 km/h, the standard deviation improved from 12.8 meters (2.3%) to 1.6 meters (0.3%). During emergency braking maneuvers at the same speed, the standard deviation fell from 16.4 meters (3.6%) to 3.3 meters (0.7%) [1]. The DCC function also successfully passed the one-year field trial.
The new WheelGrip adapt wheel slide protection system and ADM adhesion management system were also subjected to a comprehensive program of tests, both on Knorr-Bremse’s ATLAS (Advanced Test Laboratory for Adhesion-based Systems) dynamometer and on Deutsche Bahn’s advanced TrainLab (aTL) [Fig. 2]. The new wheel slide protection system matched the performance of existing systems in low-adhesion conditions (nH under the UIC standard). But in extremely low-adhesion conditions (xnH), it went on to improve adhesion utilization by between 10 and 25 percent, thus achieving even higher deceleration. In the same test conditions, the adhesion management system achieved in some cases considerable reductions in braking distances, and improved braking deceleration to a level that almost matched deceleration performance in dry braking conditions.
Assessing the potential
A study carried out by NEXTRAIL and VIA-Con on Knorr-Bremse’s behalf, using Hamburg’s S-Bahn network as a real-world example, reinforced the findings of an earlier study of RBD potential carried out in 2019: RBD is capable of shortening technical train headway times (TTHTs) [2] by valuable seconds, preventing loss of punctuality in adverse environmental conditions. Furthermore, delays caused by unfavorable adhesion conditions (e.g. autumn operating conditions) were reduced by 57 percent – a figure suggesting that a level of punctuality similar to that on dry rail is now attainable.
Subsequently, a sensitivity analysis was used to investigate the RBD effect on trains equipped with multiple levels of RBD functionality. The illustrative operating simulations showed that at a 25-percent RBD equipment level, secondary delays declined by four percent. At a 50-percent equipment level, they fell by 10 percent, and with all RBD functions 100-percent active, they fell by an impressive 20 percent. Worth noting: Taking account of the timetable’s existing contingency margins, an RBD equipment level of around 50 percent makes it possible to achieve a service quality that compares favorably with a full complement of RBD equipment.
It is already clear that TTHTs can be significantly reduced by ETCS and associated block compression techniques. But as blocks are increasingly compressed, this potential eventually comes up against its natural limits. If, however, RBD were also used, it would be possible to further reduce even supposedly minimized TTHTs, improving nominal track capacity by around 10 percent.
Figure 2: Compared to the conventional pneumatic brake, the brake force build-up time at the brake callipers is significantly reduced
Putting RBD in the context of rail as a whole
Optimizing rail operations by improving the utilization of existing infrastructure is clearly a key prerequisite for shifting traffic from road to rail. For this to happen, many different elements must be considered, such as the introduction of ETCS or ATO, the digitization of operating processes, and the clever management of passenger flows.
To maximize the benefits, all these influencing factors should be treated as an integrated system. This requires the cooperation of all those involved, from transit companies to infrastructure operators, from vehicle manufacturers and developers of signaling technology to suppliers of individual vehicle systems. Adopting such a holistic perspective undoubtedly represents a huge challenge, but the added value for the urbanized world would be enormous: City dwellers, travelers and commuters would be able to move from A to B faster and more efficiently – while benefiting from all the ecological and economic advantages of rail travel.
Author: Dr.-Ing. Marcus Fischer, M. Sc. Christopher Lozano
www.rail.knorr-bremse.com