railway-international.com
08
'23
Written on Modified on
Sustainable treatment for the ballast bed
Plasser & Theurer machines have set the international standard for high-quality ballast cleaning. They work through the entire cross section of the ballast bed. Until now, the RM 80 technology has been operated successfully in 40 countries.
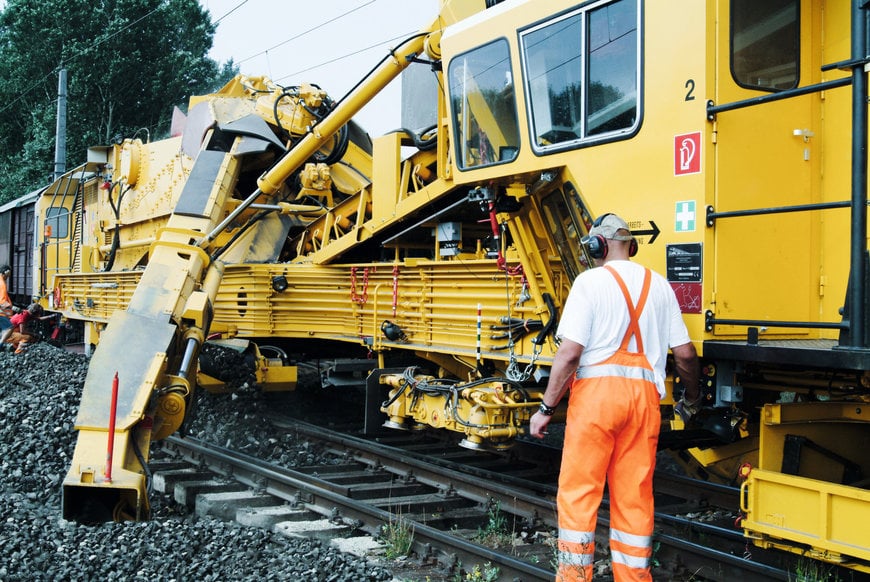
With the new Plasser ScreenLiner 3100 machine series, it has been developed further in a new, modular design. Fit for additional tasks and new regulations, the machine is configured according to customers’ exact requirements.
The aim of the Plasser ScreenLiner 3100 series is to provide high performance and quality in a compact design with sufficient reserve drive power and stability of the work units, so that the machine can be used both in short track possessions as well as in long-term operations, with equally excellent results in both cases. The series is equipped with state-of-the-art measuring and control systems, creates a precise cut of the formation, and makes it possible to recover usable ballast – an economic and environmental win-win.
Highlights in the ScreenLiner 3100 series
• High excavating capacity of up to 650 m3/h using the excavating chain with cutter bar
• Exceptional cleaning quality thanks to the triple-deck vibrating screen
• Optimized for line category C2 (EN 15528) with 20 t axle load and for the G1 structure gauge (EN 15273) when the machine is configured accordingly
• Large selection of options and enhanced features for individual customer requirements
All aboard for individual requirements and sustainable ballast cleaning
Machines in the Plasser ScreenLiner series can be enhanced with numerous features. For example, equipment for turnout cleaning, dynamic track stabilization, post-measuring, and much more can be integrated. A wide range of optional equipment ensures that the machine is individually prepared for the specific application scenarios.
More than 30% greener: transporting material on the track under repair with MFS units is environmentally friendly. This makes countless lorry runs and access road construction a thing of the past. Plus, there are fewer passes needed overall.
High cost-efficiency thanks to ModularCustomizing
One special advantage of the series is that it makes it easier to fulfil customer requirements. With Plasser ModularCustomizing, Plasser & Theurer provides components, systems, and assemblies that have been systematically standardized. The concept allows for highly configurable machines reflecting customers’ individual requirements. Standardization offers savings potential for servicing and training as well as in spare parts management. This increases the machines’ availability and economic efficiency over the entire life cycle.
www.plassertheurer.com