Reproducible Braking Distance: With this braking technology from Knorr-Bremse, trains run more often and more punctually
The growth of urban centers and rising mobility needs are placing rail transportation at the heart of the mobility of the future. With the evolution of its braking technologies, Knorr-Bremse is contributing to even more available and punctual rail transit: Reproducible Braking Distance (RBD) – achieved through the smart interaction of multiple brake components – will enable operators to increase the frequency of train services and transport more people in metropolitan areas.
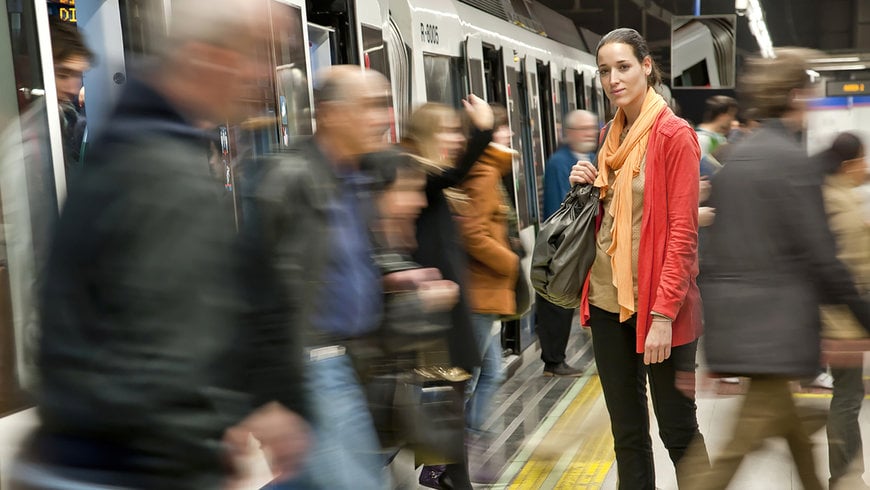
RBD technology holds significant potential for creating more mobility on existing rail (symbolic image).
- With its Reproducible Braking Distance (RBD), Knorr-Bremse is developing a pioneering braking technology to enable trains to run more often, more punctually
- Simulations on Hamburg’s commuter rail network underscore the technology’s potential: On dry rails, RBD improves transport capacity by an additional 10 percent over ETCS and Automated Train Operation (ATO)
- In adverse weather conditions, RBD significantly improves punctuality: Even on wet rails, RBD enables dry-rail levels of punctuality
- Major benefit for operators: Upgrading trains with RBD systems could help avoid expensive new track construction projects in future
A study by Knorr-Bremse, Nextrail and Via-Con, based on operational simulations on Hamburg’s commuter rail (S-Bahn) network, has once again highlighted the technology’s considerable potential.
Reduced train headway, increased capacity: simulated on Hamburg’s S-Bahn network
The partners simulated an RBD-optimized scenario and a baseline scenario (without RBD), first in dry track conditions, then in unfavorable conditions where the transfer of braking force is compromised by autumn leaves and rain. The simulations were based on a study on the introduction of the European Train Control System (ETCS) and ATO in Hamburg:
- On dry rails, RBD can further reduce train headway times and increase transport capacity by another 10 percent. So in theory, it would be possible to run 1.5 more trains per hour on the same route. When combined with ETCS und ATO, the overall potential for improvement adds up to around 40 percent of additional capacity compared with the eight train-line timetable without ETCS, ATO or RBD.
- In adverse weather conditions, the simulations showed significant improvements in punctuality. Operators could reduce uncompensated delays by up to 57 percent, so by more than half. In other words, trains fitted with RBD systems could run in adverse weather conditions almost as efficiently as if the rails were dry – in fall and winter, RBD would effectively bring “summer to the railroad”.
“These results show that in the future, Reproducible Braking Distance (RBD) technology could help improve mobility on existing rail infrastructure – especially when used in conjunction with other technologies,” concludes Matthäus Englbrecht, Vice President Global Brake Systems at Knorr-Bremse Rail Vehicle Systems. “The technology enables trains to brake more precisely, even in bad weather. This means that RBD-equipped trains could run just as safely at more frequent intervals, while at the same time reducing delays and regularizing timetables – that is, achieving the punctuality which passengers rely on. Overall, this technology represents an important building block in the automation of train operations, offering operators an attractive alternative to building new track.”
Higher capacity, greater punctuality: interesting prospects for operators
In view of the rising demand for mobility solutions, the study once again emphasizes the potential of RBD for making rail operations more available and more punctual. By upgrading their trains with RBD systems, operators will be able to increase network capacity without having to build new lines. At the same time, RBD also represents an important step on the way to automated train operation, which is already being trialed in Hamburg and is increasingly supported by various ATO systems used to assist train drivers.
Among other things, the RBD brake architecture includes a new kind of wheel slide protection – a form of ABS for trains –, as well as smart sanding systems and a deceleration control system. All these components will work intelligently together in future trains. Knorr-Bremse has already started installing smart sanding systems in certain projects, while the combined deceleration control system and adaptive wheel slide protection should be ready for series production in 2023.
The primary focus of the study is on simulating the effects of improved braking technology on train operations. Further studies are required to investigate the extent to which different levels of equipment on trains fitted with RBD will increase transport capacity (both on commuter lines and main lines). It is also important to recognize that RBD is a complex development, so the migration to RBD will continue to require close coordination between system suppliers like Knorr-Bremse, train manufacturers, regulatory agencies and rail operators.
www.knorr-Bremse.com