railway-international.com
23
'22
Written on Modified on
Driverless mobility, it's not just for metros
Alstom on Rail automation and the global supply chain.
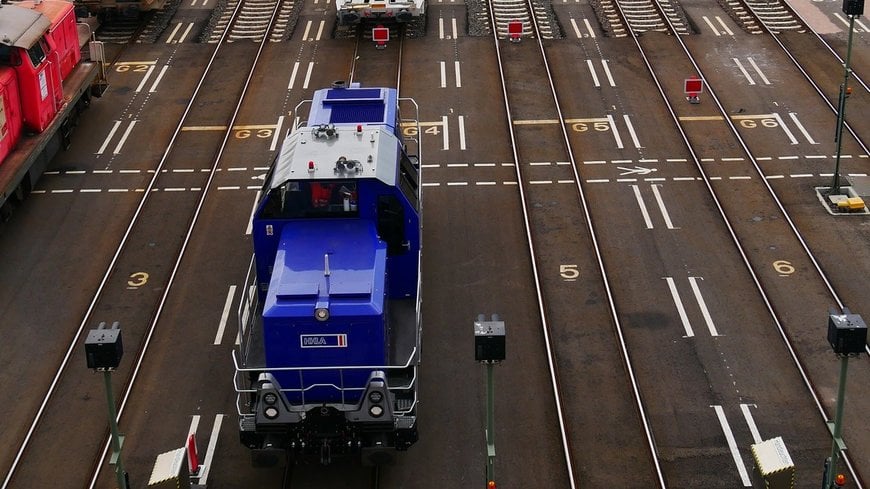
Could rail automation be the secret to unlocking logistical headaches?
In 2021, panicked headlines like “Why the Supply Chain Crisis Could Screw up Your Holiday Shopping” and “Expect Weeping Children this Holiday Season” brought the complexity and vulnerability of the world’s supply chains into focus. However, at Alstom, we are certain that railways can help address the world’s logistic challenges and rail automation is how.
When speaking of the supply chain crisis on the US’s West Coast, the US’s Transportation Secretary Pete Buttigieg said, “These issues go through the entire chain, from ship to shelf. That’s why we’re not just working with the ports. It’s the truckers, the rail companies, the operators and those retail companies that are at the other end of those supply chains.” While we can’t make ships dock faster or get them unloaded any quicker, automating locomotives could be an essential step in making the supply chains we rely upon faster, more flexible, and more reliable.
Overwhelmed ports
The first place where rail automation can help is at the ports when the containers first arrive. America’s Port of Los Angeles handles around 20% of all the USA’s cargo. In 2019 it took in around 9.3 million TEU containers (a standard container size used for truck and rail freight) and each one of those containers needs to be parked somewhere before its loaded onto trains or trucks. But easier said than done when the port of Los Angeles is so squeezed for space that it has even started fining shipping containers for sitting too long. Shortages in transport capacity means that many containers are being dropped haphazardly, called cross parking, blocking other containers from being moved and further entangling an already struggling supply chain.
Automation to the rescue
Automated locomotives like the ones we are developing in places like the Netherlands and Belgium could be the answer. Called shunting, the process of arranging various freight cars into complete trains is usually done by drivers, but it doesn’t have to be. We are working toward Grade of Automation 4 (GoA4) which is the highest level of rail automation that will enable locomotives to carry out short trips and shunting operations by themselves.
It’s a work in progress, but the signs are positive. In 2018, we successfully tested an automated locomotive (GoA2) in the Netherlands that made the trip from the Port of Rotterdam, Europe’s busiest port, to a CUP Varlburg rail terminal - without a driver.
Bernard Belvaux, Alstom Managing Director for Benelux says, “These tests will help the European rail system benefit from an increase in capacity, reduced energy consumption and cost while offering higher operational flexibility and improved punctuality.” In 2022, we plan to do it again, but in GoA4, which means completely unattended - no staff on the train.
“These tests will help the European rail system benefit from an increase in capacity, reduced energy consumption and cost while offering higher operational flexibility and improved punctuality.”
Bernard Belvaux
Alstom Managing Director for Benelux
Automation presents a real solution
This level of automation presents a real solution to the immediate global supply chain problem, but it’s also a general solution to many issues facing the world and operators. In harbours and freight yards, automated locomotives can do many of these tasks that don’t require a human driver. For example, we can automate short, menial, or repetitive trips and since the locomotives are driverless, it’s not a problem to have them standby for hours in the cold winter nights without a break.
But the potential of automated locomotives goes even further. First and foremost, automation can help drive a general trend towards more sustainable transport. As transportation accounts for around a quarter of global C02 emissions, and trains are around four or five times more energy efficient than trucks, automated locomotives represent a more sustainable choice environmentally speaking.
Trains equipped with Automatic Train Operation can also operate at closer intervals. Tighter spacing increases the capacity of the whole network and reduces its energy consumption because trains operate more uniformly. Automated operation can therefore be an added value to help operators manage increasing traffic without making expensive changes to the network’s infrastructure.
Automation also offers more flexibility
Automation also offers more flexibility. A European Union-funded study published in 2020 found that moving to newer systems for managing trains could increase the capacity of existing rail networks by up to 44%, and automation can also enable operators to extend service to remote areas where the costs of hiring a driver, or getting the driver to the location, makes such an expansion economically unviable.
And before you start to worry about robot trains taking all our jobs, the fact is that in many places the rail industry is facing a shortage of drivers. But replacing humans with machines is not the point, nor is it the goal. Rail will always need a human touch; rail automation should be seen as a support tool. Like autopilot in aircraft or self-checkout, automation is a way to leverage the power of digitalisation so our human counterparts can focus on the things that computers will never be good at.
www.alstom.com