Multi-unit axle encoders offer advantages across the entire life cycle
When a speed sensor handles more than one task.
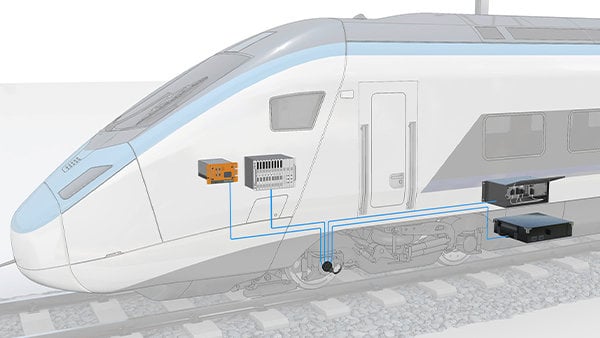
A speed sensor serves up to four sub-systems with independent encoder units.
The end of the wheel axle is needed for various functions. However, the number of axles is limited and these coveted locations may become scarce. The multi-unit axle encoders from Baumer are able to supply data to several sub-systems with a single axle encoder. When considering the entire life cycle of a train, it becomes apparent that this saves not only space but also considerable costs.
The unique multi-unit axle encoders from Baumer
Typical sensor tasks at the wheel axle include distance and speed measurements for various sub-systems, such as wheel slide protection (WSP), traction control, train control, door controls, or sensors for hot box detection and condition monitoring. Based on its many years of expertise with sensors on wheel axles, Baumer has restructured its axle encoder product portfolio. A central element is the modular structure that allows customers to integrate up to 4 totally independent encoder units in a single sensor. For example, an encoder unit is required to provide travel details to the train control system, e.g. the ETCS. The galvanic separation ensures non-interaction with other sub-systems so that they cannot interfere with or affect each other.
The separate parameterization of the individual encoder units makes it possible to select the optimum settings for each application and thus to get maximum performance out of each sub-system. This is especially beneficial for applications that have high requirements regarding signal quality and resolution (up to 1200 pulses per revolution) or for which safety-oriented behavior is essential.
The BPIV2 axle encoder with bearings can contain up to four independent encoder units and the BPIK bearingless axle encoder can contain up to two.
Simplified design
The multi-unit axle encoders offer new design options for vehicles because a single sensor can handle several functions, which is also reflected positively in the overall costs. Mechanical integration is simplified, as the axle end is standardized and fewer components are required. The greatest savings, however, are in the area of electro-mechanics – instead of up to 4 plug and cable connections, only a single connection is required.
In addition, the axle encoders from Baumer have secondary functions that support and simplify the system engineering. The function control signal serves to detect cable breaks and stop the train. The “direction of travel” signal is used by train control systems. The digital, freely configurable speed threshold is used for unlocking the door and can directly activate a relay, for example. Baumer offers a modular interface concept that allows seamless connection to most sub-systems. For example, HTL signals, HTL signals with mid voltage, a power interface, or HTL antivalent interfaces can be integrated into the sensors and configured at will. SIL-certified products are available for integration in safety-relevant systems. The sensors have been successfully tested for various suppliers of wheel slide protection systems, traction controllers, and train control systems, and they come with the required approvals and certificates.
A multi-unit axle encoder from Baumer substantially reduces the required cabling – only a single cable output is needed to supply up to four sub-systems with measurement data.
Less effort for the supply chain, mounting, and commissioning
Reducing the number of components on an axle offers considerable advantages for supply chain management, system engineering, as well as mounting and commissioning. Every connection and component entails costs and risks, which the multi-unit axle encoder reduces to a minimum.
Lower cost during operation
Defects, wear, as well as traceability can generate costs during operation. The axle encoders from Baumer support train operators in minimizing these costs.
- Defects
Most failures of the sensor technology on wheel axles are caused by defects in the connection technology, i.e., cables and plugs. A single connection lowers the risk of failure due to gravel impact, vandalism, or other external factors.
- Wear
Each axle encoder with bearings is subject to wear, and the limiting factor is often the useful life of the grease. The Baumer axle encoders with bearings, the product series BPIV2, are designed for a long service life due to the high-end ball bearings and grease that are used. The principle of a replaceable bearing package invented by Baumer allows maintenance of axle encoders in the field. Within a few minutes, the axle encoder is once again ready for use for the next 10 to 15 years. This means that the sensor technology does not have to be returned to the manufacturer for maintenance.
- Traceability
The products are labeled according to the GS1 standard. This guarantees continued and reliable traceability from the manufacturing of the sensors to the maintenance of the vehicles, while supporting all logistics, parts management, and servicing processes.
The bearing package of the BPIV2 is labeled to ensure traceability and can be quickly replaced.
The smart sensor provides signals beyond the primary function
Along with the primary function of speed and distance measurement, which are usually triggered by incremental signals (A 90 B), the axle encoders from Baumer also offer a serial interface. In addition to the digital signals such as position, speed, and angle accelerations, additional information such as the amplitude of torsional vibrations, temperatures, accelerations (x/y/z), as well as diagnosis and operating data can be retrieved. There are almost no limits to the possibilities offered. The evaluation and combination of this data with additional data of the vehicle, e.g. GNSS, opens up new possibilities for making conclusions regarding the state of the vehicle and the infrastructure.
Sensor technology from Baumer
Baumer is an international family-run company with a passion for sensor technology, rotary encoders, measurement instruments, as well as components for automated image processing for various industries and applications. For railway vehicles, Baumer provides not only sensor technology for the wheel axle, but also sensors for level, pressure, and temperature measurement as well as cameras for inspection systems in accordance with EN 501555.
www.baumer.com