railway-international.com
18
'20
Written on Modified on
Notts engineers deliver steel for HS2’s biggest tunnel site
HS2 has passed another major milestone at the high speed rail project’s first tunnel site, with the completion of structural work on the temporary pre-cast factory which will produce wall sections for the 10 mile long Chiltern tunnels.
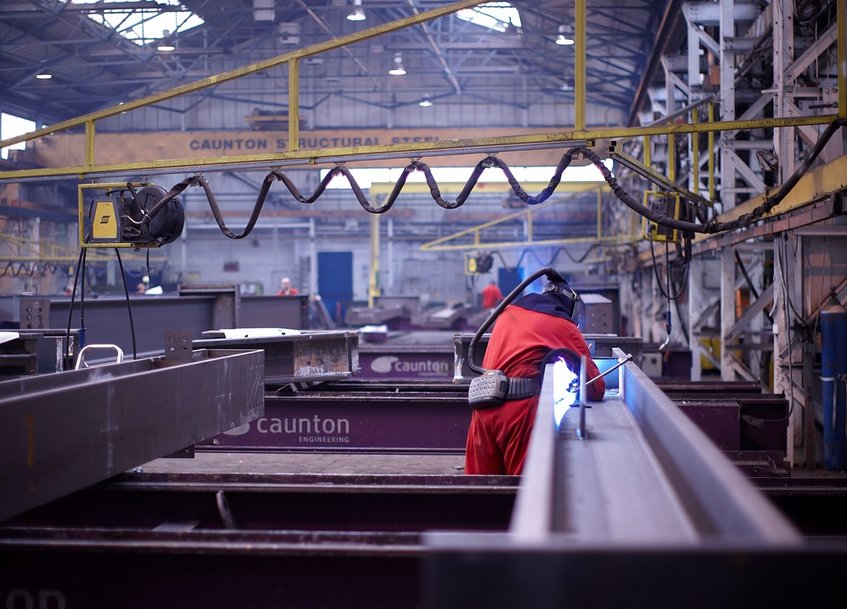
The tunnel precast factory – and all 2,400 tonnes of structural steelwork at the south portal site, next to the M25 – will be made in the UK and delivered by specialist steel fabricators, Caunton Engineering, from their base near Moorgreen, Nottinghamshire.
The factory will allow HS2’s main works contractor, Align JV - a joint venture made up of three companies: Bouygues Travaux Publics, Sir Robert McAlpine, and VolkerFitzpatrick – to cast all the tunnel segments on site and avoid putting extra HGVs onto local roads.
Two giant tunnelling machines – named Florence and Cecilia - are due to launch next year. The 170m long, 2,200 tonne machines will spend more than 3 years underground and use 112,000 concrete segments to line the tunnels, moving at a speed of 15.6m a day.
A second precast plant will be used to cast sections for the nearby Colne Valley Viaduct. Once work is complete, the pre-cast plants will be disassembled and the whole site will be landscaped with material excavated from the tunnels and trees planted in order to blend it in with the surrounding countryside.
Welcoming the milestone, HS2 Ltd’s C1 Senior Project Manager, Mark Clapp said:
“The pre-cast plant will play a crucial role in delivering the Chiltern tunnels. By casting all 112,000 segments on site, we can significantly reduce the number of HGVs on local roads, reducing disruption for the local community.
“I’d like to thank everyone at Align and especially Caunton for their hard work in making it happen. Caunton’s involvement shows how HS2 is delivering for companies right across Britain, creating jobs and helping the economy recover from the pandemic.”
Daniel Altier, the Align Project Director, said:
“Caunton Engineering is delivering the steel for all the structural buildings at our south portal site, 15 in total. This includes two tunnel pre-cast factories, the tunnel workshop and warehouse, and the viaduct precast factory. In selecting Caunton we opted for a company that can deliver a high quality product and value for money. The selection of key suppliers such as Caunton is essential in order that we can deliver the project on time and on budget.”
As well as the precast plant, Caunton Engineering are also delivering structural steelwork for the general warehouse, workshops, soil treatment plant and the viaduct pre-cast plant. In total, around 2,400 tonnes of steelwork will be delivered from their factory in Moorgreen, Nottinghamshire, on the site of the former colliery.
Caunton, which employs 250 people in the east midlands is one of the UK's leading fully automated structural steelwork contractors and a leader in 'Just in Time' manufacturing. The family-owned firm has 50 years of experience in the sector also delivered steelwork for the iconic new Museum of Liverpool.
Matthew Shimwell, Caunton’s Managing Director said:
“We are thrilled to be working with the Align team in helping to deliver this key part of infrastructure work. The project is an excellent example of how early engagement with the supply chain brings real value to a project.
“This collaborative approach has helped to optimise the design of the buildings to more fully benefit from an informed DFMA approach (Design For Manufacture and Assembly). We wish the project team every success as it enters the next key stage in delivering this prestigious project.”
www.hs2.org.uk