railway-international.com
22
'25
Written on Modified on
Bosch presents new catenary assist rail assistance system
Reduced pantograph and catenary damage increases safety, minimizes disruptions and repair costs; drivers are warned of incorrect pantograph position, and the system offers quick assistance functions for rail traffic.
www.bosch.com
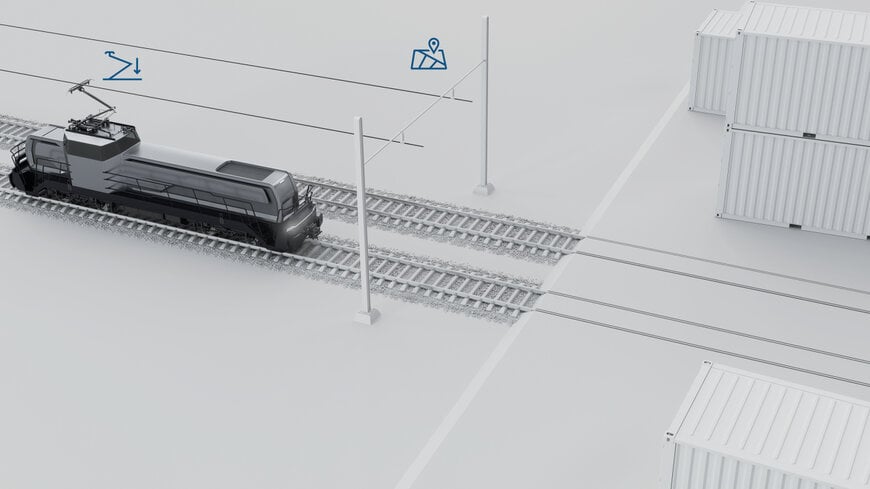
Damage to the catenary or pantograph of the locomotive is a recurring problem in railway operations and is usually caused by the pantograph being raised or lowered at the wrong time. The issue affects rail vehicles with hybrid propulsion systems, which use diesel engines or battery power on non-electrified sections and switch to electric drive on tracks with catenaries. If the pantograph is raised too early at the transition point to catenary operation or was not lowered at all, it can become entangled in the catenary system and thus cause damage. Conversely, if the pantograph remains raised, it can catch in the booms or tensioning device at the end of a catenary. Electric shocks during maintenance work near the catenary represent another source of danger. Such shocks can occur if the separation point between an active and a grounded section of the contact line is bridged by the pantograph. The new catenary assist system from Bosch Engineering can monitor the position of the pantograph and notifies the train driver of any problems in the form of an acoustic and/or visual warning.
Catenary assist consists of a control unit connected to a compact sensor system along with an antenna for the connectivity functions as well as for receiving the navigation data. In the control unit, the locomotive's position data from the satellite navigation system is processed together with the data from the on-board sensors. The system compares this data set with a stored digital track plan, thereby ensuring precise determination of the locomotive's position on the track. The map software also indicates whether the pantograph can be raised on the respective track section. If the current pantograph position differs from the prescribed state, the train driver receives a warning message in the cab. A remote function also allows the messages from the assistance system to be displayed on an external control panel, for example, if the train driver remotely controls the locomotive from the track for precise shunting operations.
Catenary assist is designed as an independent assistance system that requires no interfaces to the train vehicle other than the power supply. Thanks to the modular design of the system components, it is suitable both as original equipment for new locomotives and as a retrofit option for existing fleets. Bosch Engineering thus offers rail operators a quick and easy entry point into the world of assistance systems for rail vehicles. For customers requiring a more comprehensive set of functions, such as predictive monitoring of the entire locomotive surroundings, Bosch Engineering has developed the rail assist suite. This technology combines camera, radar, LiDAR, and ultrasonic systems of the latest generation, meaning that the integrated catenary assist also supports sensor-based detection of the contact line signals, among other functions.
www.bosch-presse.de