Responding to Customer Needs
The Development of Wheel Sensor RSR110 and Frauscher Track Vacancy System FTVS.
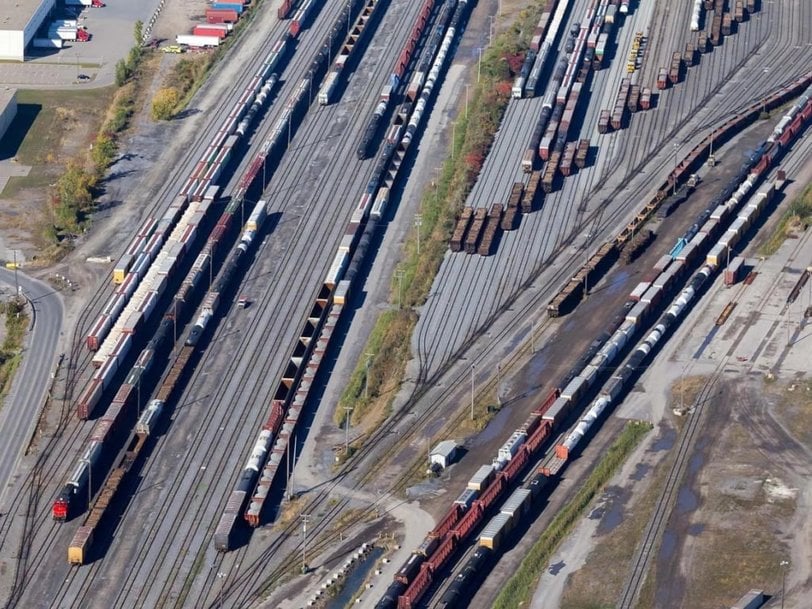
In today’s dynamic landscape, technological progress and advancement is unfolding at a considerable speed.
Consequently, there is a requirement for companies to continuously innovate and adapt to the evolving needs of customers to maintain and further bolster their market position. Since its establishment in 1987, Frauscher Sensor Technology has positioned itself as a market leader within its segment and has consistently prioritised the fostering of close communication and collaboration with its valued customers, while staying closely attuned to the requirements of the broader rail industry. On numerous occasions, this commitment has culminated in the creation of innovative products or systems: one such example is the development of the Frauscher Track Vacancy System which represents a cost-efficient axle counting solution, ideal for non-vital applications.
Global Adoption: Axle Counters as a Proven Technology
Throughout past decades, the use of axle counters within signalling systems has grown exponentially across the world. This is due to their overall reliability and flexibility which has enabled them to accommodate a diverse range of projects and customer needs across various applications such as track vacancy detection, switch point protection, level crossing protection and many others. Due to these characteristics, axle counters constitute vital components of modern signalling systems, playing an essential role in ensuring the safety and efficiency of rail operations.
The RSR110 Forms the Basis of the Frauscher Track Vacancy System FTVS
The development of the FrauscherWheel Sensor RSR110 represents a significant step in fulfilling the need for wheel detection in non-vital applications. The RSR110 offers a cost-effective and efficient solution for non-vital applications due to its versatility which means it can be seamlessly integrated into any system. This wheel sensor also forms an important part of the Frauscher Track Vacancy System FTVS, alongside the Wheel Signal Converter WSC and the Wheel Counting Board WCB.
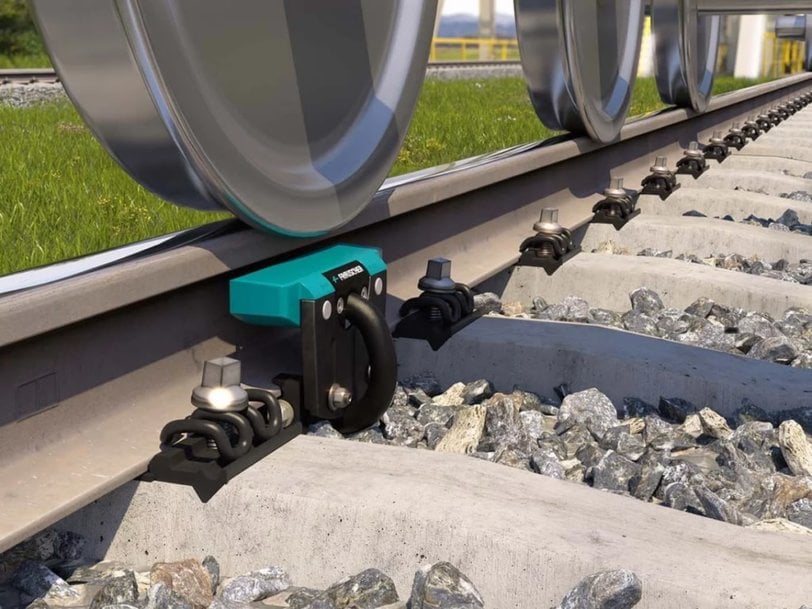
The robust nature of the RSR110 means the sensor provides reliable wheel detection even in adverse conditions. Its easy installation, minimal maintenance requirements, and low lifecycle costs contribute to the overall efficiency and cost advantages for users. Furthermore, the RSR110 is rated at IP68 which guarantees a total protection against water ingress for more than 30 minutes with depths up to one meter, making it an ideal solution in projects with frequent flooding at the trackside. The Wheel Sensor RSR110 thus delivers a dependable and flexible solution for various non-vital rail applications and has been a tried and tested solution in projects worldwide. Furthermore, thanks to the patented Frauscher Rail Claw, the installation of this sensor can be carried out quickly and easily without the need to drill holes into the rail which lowers the costs associated with mounting and reduces the dwell time of engineers on track.
In the case of the FTVS, the Frauscher Wheel Sensor Signal Converter WSC is used to digitalise the wheel sensor information, converting the analogue output received from the RSR110 into digital pulses. The Wheel Counting Board WCB then uses this information to provide clear and occupied status outputs for a specified track section.
The Frauscher Track Vacancy System FTVS as a Cost-Efficient Solution for Non-vital Applications
Due to its wide array of benefits, the RSR110 gradually became widely used for many non-vital applications, for instance in yards, for purposes such as storage track monitoring, switch protection, door opening and much more. Operators had become accustomed to its reliability and overall performance, especially in areas where conditions or weather were suboptimal. The acceptance of this sensor as a robust and reliable product eventually led to development of the Frauscher Track Vacancy System FTVS.
The FTVS is an axle counting system for non-vital applications that consists of three components: the wheel sensor signal converter WSC, the wheel sensor counting board WCB, and the aforementioned Wheel Sensor RSR110. The WSC is tasked with converting the analogue output provided by the RSR110 into a digital signal, which is used to feed into the WCB for the purposes of axle counting.
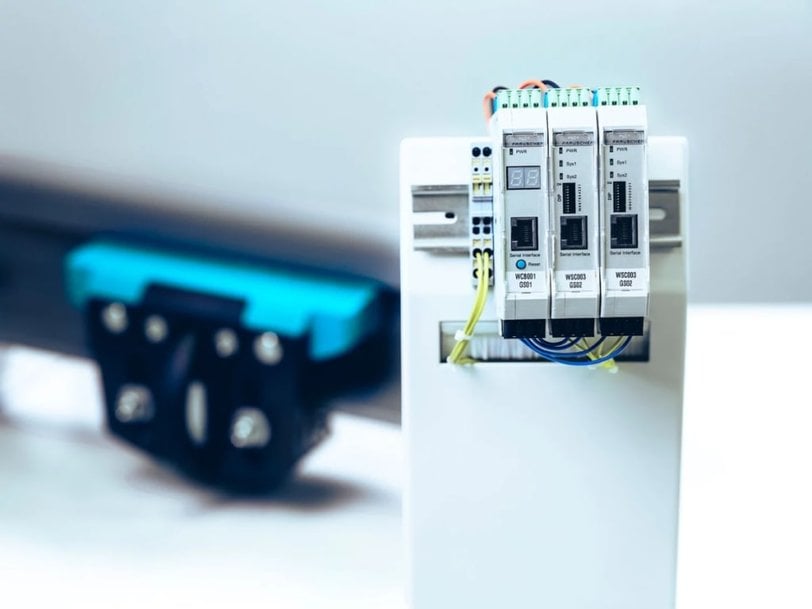
The WSC provides two outputs that can be configured with the FTVS: the first output is used as system digital pulse input to the WCB for axle counting and the second output can be used in combination for direction information or center or gate pulse. The function of the WCB primarily consists of counting the axles which move in and out of a specified track section to determine if the section is clear or occupied – this is done on the basis of the digital signal provided by the WSC.
The simple architecture and core features of the FTVS present the operator with a multitude of benefits, including:
Reliability in all types of adverse weather and track conditions
Easy and convenient installation alongside low maintenance costs
Possibility for installation in tight spaces due to a limited number of components
DIN rail mount requires minimal space in wayside enclosures
No dead sections or electrical isolation required
Suitability for a wide array of non-vital applications such as switch point protection in yard
The FTVS is therefore suitable for operators who require a highly available and reliable non-safety critical system without the need for advanced features which are offered with Frauscher’s vital SIL4 axle counter, the Frauscher Advanced Counter FAdC®. Given its versatile nature, the FTVS is particularly useful in areas such as yards, industrial facilities, and ports where unsatisfactory operating conditions can negatively impact the performance of track circuits, or where trackside and wayside space constraints make their use difficult.
The interest in the FTVS is continuously expanding, fueled by demand from various rail operators across many different locations and countries. In line with this, the list and scope of potential applications for the FTVS is also increasing: a good example of this is the utilisation of the FTVS as a low maintenance, cost effective solution for non-vital level crossing protection.
www.frauscher.com