railway-international.com
27
'24
Written on Modified on
Integrated CMCO solution expertise for railways worldwide
Since Pfaff Verkehrstechnik was fully merged into Columbus McKinnon (CMCO) in mid-2023, integration within the Group and the mutual support of the Group’s various brands has been further strengthened.
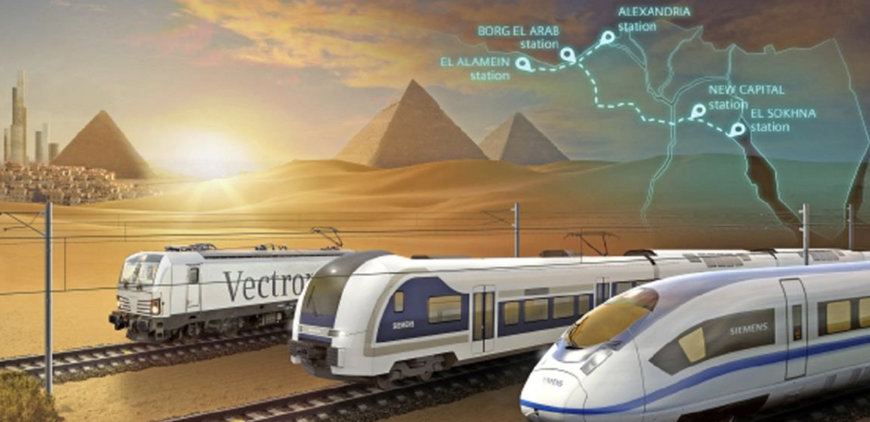
When it comes to project execution, it is not only Columbus McKinnon Engineered Products with its Pfaff-silberblau brand that is involved – STAHL CraneSystems and YALE also play their part in the success of the projects. Cooperation within the Group results in new outstanding railway technology solutions, which are realised worldwide together with local partners and subcontractors.
The portfolio of the former Pfaff Verkehrstechnik continues to be expanded under the umbrella of CMCO. Sister brands YALE and STAHL CraneSystems also make a strong contribution towards implementing specialised railway technology solutions. These include transport components, but also the complete planning, installation and maintenance of turnkey lifting systems for a wide range of railway projects worldwide.
With the combination of brands and increasing integration, CMCO is best placed to fulfil customer and market requirements. Under a single umbrella, the individual brands complement each other perfectly, as CMCO continues to develop as a reliable technology partner for transport engineering and beyond. Railway technology customers receive all products, solutions and services from a single source, with simpler and efficient processing from order to delivery and customer service. At the same time, customers benefit from a significantly larger product portfolio. A newly established after-sales service team offers even more comprehensive and faster support.
Diverse projects in Europe
A huge number of major projects have been realised or are underway worldwide. In India alone, large projects are currently in progress at eight different locations, including Delhi, Pune, Bangalore and Mumbai. CMCO is highly active in Europe too – for example for the German Eiffage Group, which requires a Wi-Fi controlled system (10 lifting units for 30 tonnes each) for lifting maintenance vehicles and track-laying machines over a length of up to 110m.
In recent years, for Swiss Federal Railways, existing rail platforms in Basel have been upgraded with roof working platforms, crane rails and service lifts. Skanska AB, a Swedish multinational construction company, also uses CMCO technology – for example to equip a depot in Sävenäs, Gothenburg, including 25-tonne lifting jacks on a rail-guided lifting system with automated laser tracker positioning.
“Make in India” projects
CMCO recently delivered an underfloor lifting system to an Indian customer, HYT Engineering Company. It was manufactured under the “Make in India” initiative, i.e. more than 50% of the production was carried out in India. For the first time, the factory acceptance test of an underfloor lifting system including load tests was carried out on site in India, and was approved in Ahmedabad at the first attempt without any defects. To meet the requirements of the initiative and factory acceptance, Pfaff Verkehrstechnik cooperates with local manufacturing partners, such as STAHL India, part of Columbus McKinnon, and Techno Industries, a leading Indian manufacturer of cranes, lifts and escalators.
The system is used to service and maintain eight-car Vande Bharat trains. The end user of the lifting system is the state-owned railway company Indian Railways, which operates most of India’s rail transport. The underfloor lifting systems comply with the highest international safety regulations, such as the EN 1493 European standard for vehicle lifts. Delivery in pre-assembled modules minimises assembly times on site. Thanks to this system, the Vande Bharat trains can be maintained in a much shorter time than before. Due to short set-up times, the vehicles are quickly ready for operation again, and their operating times in transport use are extended. CMCO’s other projects in India include lifting systems for the Pune metro and Kanpur metro.
Major projects in Israel
Desiro HC (High Capacity) electric trains made by Siemens Mobility are maintained at the railway depot in Ashkelon, Israel. CMCO has provided solutions to fully equip the depot’s workshop. In addition to track systems, these include an axle changing system, multiple lifting tables, mobile lifting jacks, hydraulic support jacks, turntables and roof working platforms (“flying carpets”) for maintenance work on the train roofs. Twenty-four mobile lifting jacks each with a load capacity of 20 t are used to lift up whole trains for maintenance and servicing work. The entire lifting jack system is controlled by frequency converters. Synchronisation of the individual lifting jacks makes it possible to lift a train with a precision of ± 4 mm.
For maintenance and repair work on the train roofs, all three maintenance tracks were equipped with “flying carpets” by CMCO subsidiary STAHL CraneSystems. These cradles are suspended from crane runways on the workshop ceiling. They can be moved over an extensive range of 175 m along the entire length of the workshop and thus along the entire length of the train. Each “flying carpet” has two hydraulically lowerable gondolas that can be operated either as a pair or individually.
The gondolas have electric extension modules to bridge the gap to the train and thus facilitate access to the roof. Telescopic guardrails can be used to secure the working area all around for safe working on the roof. To simplify the removal of components and their onward transport, vertically movable cranes were installed between the gondolas. These can also be controlled remotely via radio control.
Railway technology in Peru
CMCO has supplied workshop equipment system components for the new Santa Anita depot for the Lima metro in Peru. The entire equipment was installed together with Berlin-based company SIM IMPEX, and includes an underfloor lifting system as well as bogie lifting stands, axle lifting systems (underfloor), mobile lifting jacks, manual turntables, lifting and turning equipment for bogie frames, auxiliary bogies and transport devices in large quantities.
The underfloor lifting system from Pfaff Verkehrstechnik is designed for heavy trains of up to 280 tonnes with up to seven carriages and a total length of 120 m. The synchronisation of the wheel lifting platforms is controlled by a programmable logic controller (PLC) within a narrow tolerance range of ± 5 mm, i.e. over the entire length, the maximum height deviation of the lifting platforms is only 10 mm. Their cantilever design ensures that the removed bogies can be pushed out from under the lifted train for separate maintenance.
Major Siemens order in Egypt
Two years ago, Siemens announced it had received the largest order in the company’s history, from Egypt. The order includes 41 eight-car Velaro high-speed trains, 94 four-car Desiro High Capacity regional trains, and 41 Vectron freight locomotives. Siemens Mobility will provide the latest technology platforms to optimise train operations, the rail infrastructure and subsystems throughout the network.
The “Green Line” is serviced at the October Gardens depot (west Cairo) to ensure maximum availability. Here too, CMCO has supplied numerous system parts, components and other equipment for the maintenance of the rail vehicles, including underfloor lifting systems for the Velaro and Desiro trains. In addition, lifting and turning equipment for bogies, wheelset changing systems, lifting stands, working platforms, and overhead cranes from STAHL CraneSystems have been installed.
All-round expertise: hydraulic solutions from YALE
In the German rail transport network, Deutsche Bahn uses lifting solutions from YALE, including small hydraulic pumps, to maintain the bogies on DB Regio trains. A PYB cordless battery powered pump together with the YALE YLS-20/45 low-profile cylinder slightly lifts the train by a little over 2 mm so that the wheels can be turned and checked for damage – this is an official railway maintenance procedure that used to be done by hand.
Deutsche Bahn has now opted for the mobile solution with the PYB cordless battery powered pump, which can develop an operating pressure of up to 700 bar. Applications include the operation of small to medium-sized cylinders, such as the YLS single-acting low-profile cylinder with a lifting capacity of 10 to 100 tonnes and a spring return. Such cylinders are ideal wherever space is limited. They are mainly used for lifting, positioning and clamping.
Normally, the bogie is lifted from at least four points – with this solution, it is sufficient to lift it on one side (i.e. slightly tilted) because the wheel only has to be rotated once to check for damage and cracks, for example. However, the CMCO solution also allows the entire bogie to be lifted, by simply replacing the 2-way distributor with a 4-way distributor.
www.cmco.com