railway-international.com
04
'23
Written on Modified on
Harnessing 3D printing technology to deliver fast and sustainable rail parts
Chances are that if you’ve travelled on an Alstom train, that train has one or more of its parts created by 3D printing, also known as additive manufacturing.
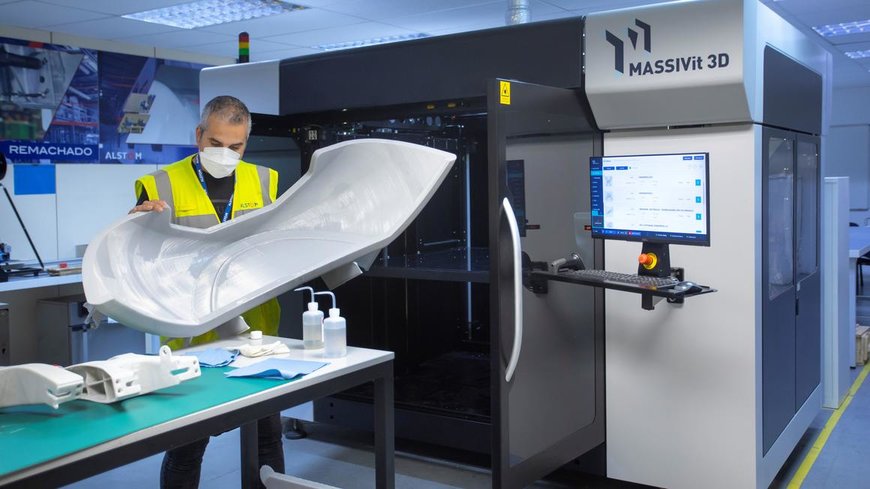
n fact, we’ve just reached the milestone of having produced 150,000 3D-printed parts. Aurelien Fussel, Head of Additive Manufacturing Program, answers questions on Alstom’s exponential embrace of additive manufacturing solutions.
Aurelien Fussel, head of Alstom’s additive manufacturing industrial program, has been driving the company’s strategic adoption of 3D printing for eight years. Aurelien has built Alstom’s program from the ground up, supporting change management, expanding the types of printing materials used, creating the digital warehouse, growing the 3D-printed spare parts business, leading expertise and much more. Aurelien has been at Alstom since 2007 and has been in various managerial positions related to projects (tramways in La Rochelle, Los Teques2 Metro in Valenciennes Petite-Forêt), innovation, quality, and special process management.
How long has Alstom been using 3D printing technology?
Back in 2016 there was just me with a small 3D print machine printing some pen holders. Things have really changed since then! 3D printing quickly became one of Alstom’s special processes. We started with a couple of parts and materials, and today there’s an exponential curve in the number of parts we print with this technology – not to mention the savings we are generating. Over the last two years, we have produced, annually, about 40,000 parts, including machine tools and jigs, spare parts, missing parts, and new designs.
What types of spare parts can Alstom produce using 3D printing?
We can print three types of materials: polymers, ceramics and metal. We have about 20 validated polymers (including fire and smoke compliant ones – EN45545 for Europe and NFPA130 for North America) and four metals: aluminium, stainless steel, high-performance steel and titanium. The range of parts is impressive: for example, we’ve just produced a headlamp case for a new high-speed train in France, a jig to ease screwing holes in carbody shells in Germany, a part in a soft material for an air conditioning evacuation tube for a metro project in Spain, and a steel cover for a bogie in the Nordics.
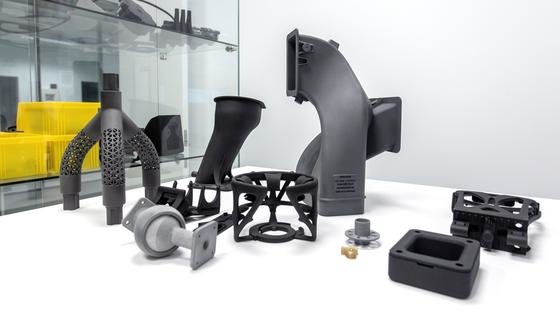
Alstom's team can print many different parts directly in our depots around the world - from battery locks and broken connectors to replacement of a damaged front end, additive manufacturing has become a critical tool for spare parts
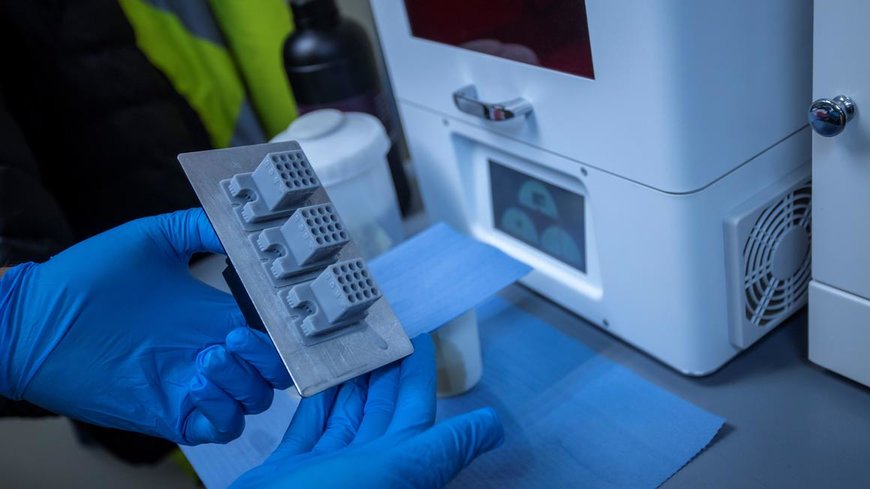
What are the advantages of additive manufacturing?
The first argument is the lead time. Customers know that when they select additive manufacturing to print a part, we do our best to be faster than the conventional technologies.
Secondly, it’s more economical because there is no minimum order quantity. For example, we had a recent order for 40 curtain hooks for train interiors. If the customer had asked the manufacturer, the manufacturer would have said they needed to order 500 hooks. With additive manufacturing, it is more expensive for each part, but for an order of just 40 it works out less expensive to 3D print them. Depending on the size of the part, the break-even point for plastic is about 2,000 parts and for metal it is about 200. It’s a new tool in the engineering toolbox that, for some areas of business such as spare parts, is a relevant solution.
The third advantage is hard inventory reduction. In the example I’ve just given, using conventional technology, the customer would have had more spare parts than they needed immediately. Those parts would have to be stored, sometimes for years, in the depot store. Customers want to reduce the footprint of their warehouses. With Alstom, they can have a ‘digital warehouse’, and we can offer what we call ‘on-demand spares’.
Lastly, 3D printing is more sustainable, because it uses less material than conventional technology: there is less scrap. The process also uses less energy because we can produce only the quantity needed. In the future, when each tonne of CO2 may have a fixed cost, 3D printing will be a game changer.
How large is Alstom’s 3D printing network?
For the past six months, I have been able to say that the sun doesn't go down on additive manufacturing within Alstom. We have 3D printing hubs in Saint Bruno, Canada; Barcelona, Spain; Sesto San Giovanni, Italy; Bangalore, India; Valenciennes and Tarbes in France; Hennigsdorf and Salzgitter in Germany; Istanbul, Türkiye; and Singapore. We have 150 machines now. In addition, we have, as a minimum, one supplier per region. If we are asked to print a few parts, we can do that in-house, but for thousands of parts, we subcontract to one of our qualified suppliers. In the next few months, extra-large prints using robots will be possible – stay tuned!
How does Alstom see the 3D printing market evolving in the future?
Already, we can see the new business of digital warehousing emerging. With 20% of the parts in a train now printable, operators are moving faster than ever to adopt this technology. The world of tomorrow will be more data-centric. We can send digital files of parts around the world and print parts as close as possible to the customer. This contrasts with today, where we might buy raw material in the Far East, manufacture in Europe and sell, say, a carbody shell to North America. With digital printing, we eliminate customs taxes, massively reduce lead times and fulfil local manufacturing contract needs.
www.alstom.com