railway-international.com
22
'23
Written on Modified on
DIGITAL SLEUTH IN ACTION AT DB CARGO
DB Cargo is testing "Spot", a walking robot that helps with train maintenance.
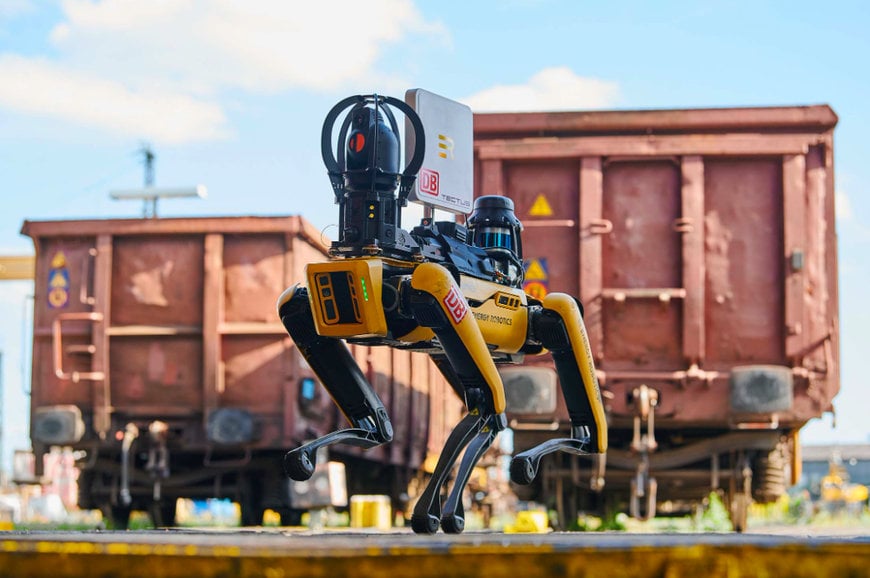
In order for more goods to be transported by rail, there must be enough vehicles available - this means a high level of maintenance. Digitalization is also central to a successful transport transition in this area: digital tools ensure more effective maintenance and get trains back on the route more quickly. Train pit stops will be shortened, creating more capacity for transporting goods at short notice. An example of such a digital tool is the walking robot “Spot”. It was presented for the first time at the Mainz freight station in a DB-specific environment for wagon location and axle shaft inspection.
Digitalization is radically changing vehicle maintenance. It makes it possible to relieve employees of time-consuming routine checks and thus free up time for important repair work. Several tools are already helping DB Cargo, such as the automated wheelset measuring system, camera bridges with artificial intelligence and underfloor robots. A new addition is the walking robot “Spot”: Equipped with highly developed cameras, sensors and AI, “Spot” can identify freight wagons and carry out visual inspections to detect damage to the train.
The four-legged robot, which is reminiscent of a dog, is an industrial product with cutting-edge technology from Boston Dynamics. It can be used in various places that are difficult or dangerous for people to reach - such as the area under trains. The remote maintenance software comes from the German startup Energy Robotics, which adapts the system to DB-specific requirements and rents it out as a “Robot as a Service”. “Spot” weighs 25 kilograms, is 84 centimetres high and can reach speeds of up to 6 kilometres per hour. It is also very robust and has a level of agility that has never been achieved before. After being presented at InnoTrans 2022, the walking robot will now be used in a DB-specific environment for the first time.
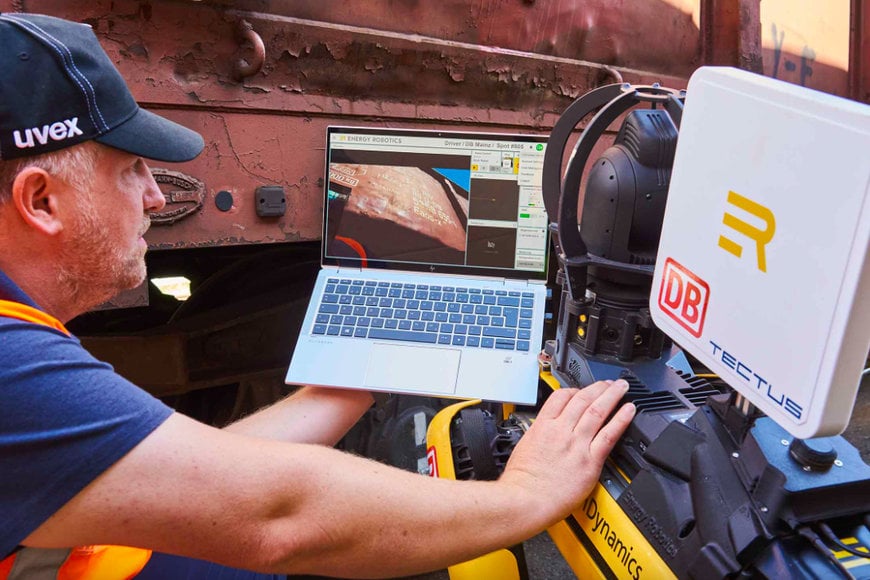
In a six-week test, “Spot” will be tested in two use cases: First, wagon location using RFID (a method for automatically identifying objects via radio) and text recognition will be tested on two tracks. Afterwards, a visual inspection of axles from the maintenance pit of the freight car workshop is on the agenda. The walking robot can reduce walking distances by 50 percent, objectify test results and increase safety by eliminating mining work. Employees are relieved of physically demanding work and gain time for value-adding activities. In this way, maintenance costs can be reduced and the shortage of skilled workers can be cushioned. If “Spot” proves successful, he could carry out these tasks in four DB Cargo plants in the future take over. The use can also be extended to other applications, such as detecting loose brake hoses and leaks on freight wagons.
www.dbcargo.com