railway-international.com
11
'23
Written on Modified on
Track Damage Detected Precisely: ZF Presents Track Monitoring for Digital Track Inspection
New function extends connect@rail condition monitoring system with infrastructure monitoring.
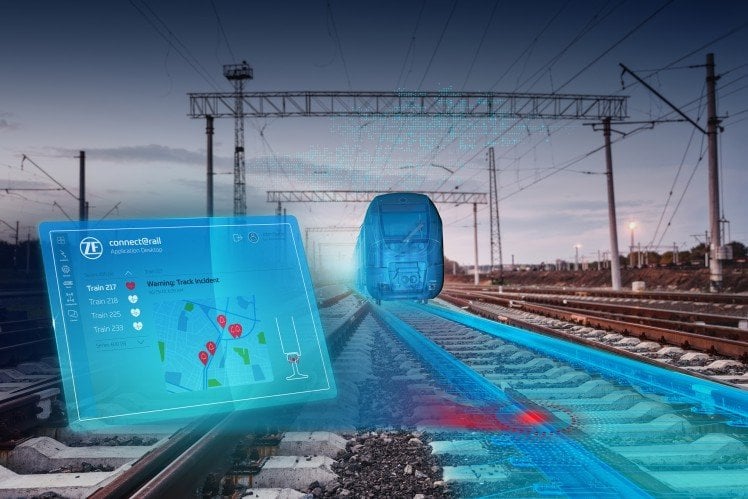
Whether cracks, corrugation, fractures or spalling: Even apparently minor defects on the track can have serious consequences. Train operators must therefore continuously maintain their rail network. Knowing where and when maintenance work is necessary is therefore essential for smooth operation. ZF supports this with the new track monitoring function of connect@rail, the digital platform for condition monitoring. Track monitoring helps transport associations and railway companies to determine the precise location of potential track damage, thus increasing safety and travel comfort.
A rail will take a fair share of battering over the years. Around 3,500 kilometers of track within the German rail network (equaling more or less 10 per cent) are currently considered overburdened. These sections alone account for around 235 million train kilometers per year. And the figure is expected to surge even further. It is therefore all the more important to keep this infrastructure in good shape. "ZF is optimally positioned to support our customers in this important and complex task. To do this, we combine our many years of industry expertise with our digital know-how," says Alan Dittrich, Head of Digital Solutions for Rail at ZF, on the margins of the Railway Forum conference. There, the company will present the new track monitoring feature, which will soon be part of connect@rail, the all-in-one digital solution for modular condition monitoring in rail transport.
Track damage: minor defects, major consequences
"Damage to the rail may seem to laypersons like the usual signs of wear. But looks can be deceiving," says Dittrich. An average regional train weighs around 120 tons on average and often tops out at 160 kilometers per hour. "With loads like this, any fracture, corrugation, spalling or edge crack can have enormous consequences," explains Dittrich. These and other defects are the cause of derailment in half of all cases. But even if it doesn't come to an extreme situation, passengers suffer from poor track maintenance. For rail defects lead to annoying noise and vibrations in the passenger car, which reduces travel comfort. Previous inspection solutions – in particular those involving search teams that patrol the network on foot – have been time-consuming and cost-intensive. With the track monitoring feature of connect@rail, ZF offers a comparatively simple yet precise solution.
The heat map: colors make damage visible
Track monitoring is based on ZF's existing connect@rail condition monitoring system, which has many years of successful operation behind it. The new functionality consists of three core components: Bluetooth-based sensors, telematics gateways and cloud connectivity including data visualization in a user-friendly dashboard. Two Heavy Duty TAGs – one sensor per wheel – are placed on the bogie near the axle. There, they record acceleration data in real time, which is collected in the VCU Pro Onboard Unit gateways and sent to the ZF Cloud. This is where an algorithm steps in that can identify possible track damage from minimal deviations and patterns in the data and precisely locate it in the rail network thanks to the GPS function of the sensors.
The collected data is then visualized in the form of a heat map via the customer-specific dashboard. The different colors tell the rail operator which parts of the rail network are potentially affected. "This provides our customers with pinpointed, specific and timely maintenance information, which greatly simplifies track maintenance and brings economic benefits – not to mention comfort and safety for passengers," explains Dittrich. The next generation of the technology will aim not only to identify the location but also the types of defects. "To this end, we are currently collecting and labeling large amounts of data in order to subsequently calibrate the algorithm accordingly." One more plus: connect@rail is also available as a retrofit solution. This allows operators to benefit from ZF's digital solutions without having to renew their fleet.
ZF plans to bring track monitoring to the market next year. The company is currently working with a South German short-haul transport association that has equipped three vehicles with the new feature. At present, the trains are running in normal operation. A win-win situation: In this way, ZF can collect real data for the next development steps, and the cooperation partner is supported in the rail inspection.
www.zf.com