railway-international.com
04
'22
Written on Modified on
New modern aluminum welding line in Alstom’s Wroclaw site will give jobs to 100 more people and enable new projects
Alstom, a global leader in smart and sustainable mobility and the largest manufacturer and exporter of the Polish railroad industry, has launched an aluminum welding line at its rolling stock site in Wroclaw.
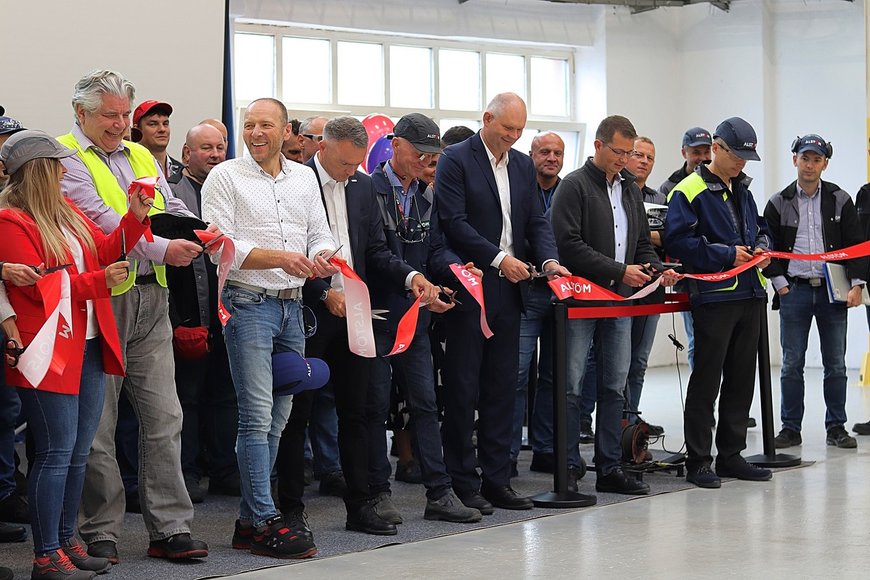
Aluminum is increasingly used in rail, extending the life of railcars to about 40 years.
This investment is in line with the company's sustainable mobility strategy and with trends in the development of the rail industry - replacing heavier and more difficult-to-machine steel with lighter and more efficient aluminum in many respects. For example, high strength-to-weight ratio and resistance to corrosion.
The new aluminum welding line will create at least 100 new jobs at Alstom's Wroclaw plant, and is linked to investments of almost €10 million, including new equipment and machinery, adaptation of the plant's infrastructure to the new technology, and employee training. Ultimately, the investment will enable the Alstom plant in Wroclaw to acquire new projects and produce aluminum boxes for regional trains for European markets.
At the same time, thanks to this investment, the competencies of the plant's employees from various departments will be developed. Implementation of new technology in Wroclaw is actively supported by the Chorzow-based Alstom Konstal, which has been an expert in aluminum welding for many years and successfully produces complete vehicles for foreign carriers: POP regional trains for Italy's Trenitalia or ICNG trains for the Netherlands.
“Alstom is at the forefront of aluminum welding technology in rolling stock production in Poland and will continue to develop and popularise this technology, which is more efficient and environmentally friendly than conventional steel. Aluminum has many advantages over stainless steel in train construction. Aluminum guarantees a lower weight of trains, which in turn contributes to using less energy to power the train and thus lower CO2 emissions. At the same time, the reduced weight of the carriage means that train speeds can be higher even on existing railroad tracks,” said Slawomir Cyza, President and Managing Director of Alstom in Poland, Ukraine and the Baltic States.
The rail industry is increasingly moving away from the use of steel and replacing it with aluminum as the primary material for trains. This is a consequence of the innovations transfer from the aerospace industry, where the pressure to develop low-weight materials is great, and the adaptation of them by the rail industry. Aluminum has high formability - it can be easily machined into any shape, and excess material is fully recyclable. This shortens the production cycle of trains.
The Wroclaw site has unique technological competence and is a leading manufacturer of locomotive and passenger vehicle bodies, including bodies for high-speed trains. Bogie frames for various types of rail vehicles are also being built there. The total value of ongoing projects is nearly €700 million, and the site employs more than 1,000 people. The new aluminum welding line will further expand the site's projects portfolio.
Alstom™ is a trademark of the Alstom Group