railway-international.com
12
'21
Written on Modified on
Plasser & Theurer embraces innovative 3D simulation
Tamping and ploughing go digital
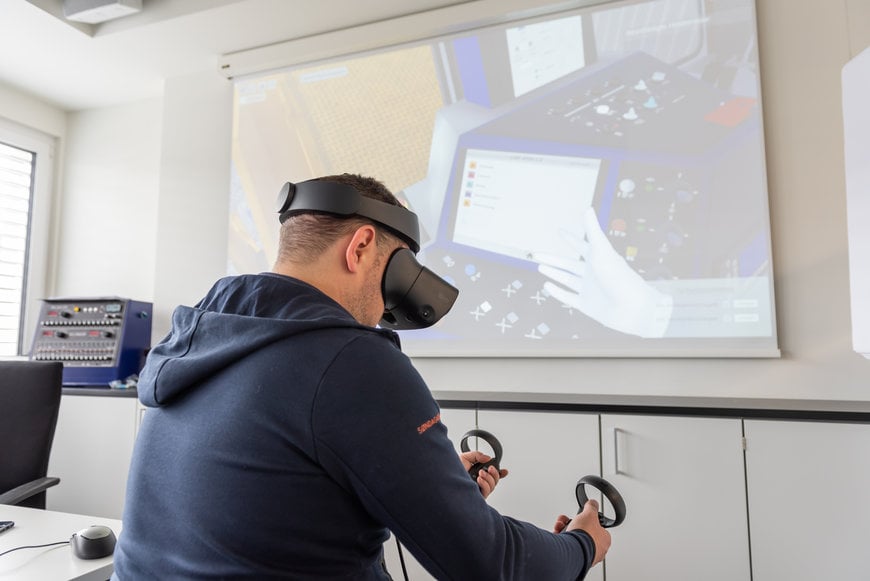
Aviation is not the only sector that uses modern simulation technology - the Austrian global market leader for track maintenance machines also uses it for seminars and training courses. The VR ballast regulating simulator represents a new generation of 3D simulation technology.
Modern track maintenance is characterised by complex machinery. Its work output and work quality are contingent on its operating staff’s qualifications. That’s why Plasser & Theurer started using innovative, efficient instruction and training methods early on. The development of 3D simulators has been ongoing since nearly ten years. They allow you to train your skills in operating entire machines without the risk of harming the machine or infrastructure. Operating errors may cause significant damage, especially in the early stages of training.
2011: the year of the first 3D simulator for track maintenance machines
The first stationary simulator was built back in 2011. Trainees would sit down in a detailed replica of a tamping machine's work cab. They used the control elements built into the armrests of the seat, the original operating desk, and the touch panel for the CWS computer working system; the tactile aspect was completely realistic. As is the case with the actual machine, they operated the tamping unit with a pedal. The first simulation model offered a variety of track-tamping scenarios in which trainees had to showcase their skills: mastering obstacles such as level crossings, inductive track magnets, cable ducts, or signal switching mechanisms.
New technologies enhance the range of training options
The first simulator used rear projectors to visualise processes; this technology is relatively expensive and requires a great deal of space. The next generation used modern displays instead. As a result, all of the technology could fit into a mobile container. In addition to the work cab, it also simulated a front cab. This also allowed trainees to practise commissioning and driving a tamping machine.
This first mobile 3D simulator was presented at iaf, the International Exhibition for Track Technology, in Münster, Germany in 2013. Two years later, the first 3D simulator for turnout tamping machines followed. Its development allowed users to train in far more complex working conditions. Motivated by its successful operation in Germany and Austria, Plasser & Theurer's international partner companies also opted to use simulation technology. In 2015, Plasser American received a simulator for the GRM 3000 compact tamping machine. In 2017, Plasser India put the stationary simulator for a 09-3X track tamping machine into operation.
Simulation technology goes beyond training
One notable aspect, and one which should not be underestimated in the future, is the use of simulation technology in settings that are not related to training. For example, it was used in the development of “PlasserSmartTamping – The Assistant”, a turnout tamping assistance system. This technology is the first major step towards automated tamping. Specifically, the 09-4x4/4S turnout tamping simulator was used here, serving as the turnout tamping machine’s “virtual twin”. As a result, development cost savings were significantly higher. These funds would have been needed for test procedures with real machines otherwise.
The latest simulation technology for ballast regulating machines
Developing and building individual 3D simulators is a costly undertaking. For that reason, Plasser & Theurer always endeavours to keep these expenses to a minimum. A major advancement in this direction was successfully designing the first VR ballast regulating simulator. This simulator was the first to combine software with VR glasses. Trainees simply put on the VR glasses and enter commands using a controller. A space of 3 m2 per person is sufficient. This simpler equipment makes the new generation of simulators much more affordable as well as more mobile, thereby ensuring greater flexibility.
The VR ballast regulating simulator is not only suitable for Plasser & Theurer’s larger ballast regulating machines: it can also be used for machines with fewer functions available. As a result, the simulator lends itself to almost all of our current ballast distributing and profiling machines.
Training in ten-day intervals
Approximately 3,500 machine operating employees have attended the Linz Training Centre in the last ten years. In the past, most practical training took place on the customer’s premises. Today, all trainees acquire their first practical experience using tamping machines on the simulators in Linz. Performing the first tasks on the new machine is easier, quicker, and safer as a result. According to Plasser & Theurer's Customer Services, this aspect highlights the advantages of simulation technology. It offers proof that the following aim has been achieved: to increase operating staff’s qualifications in an efficient way and, as a result, to make machine operation even more cost-effective.
www.plassertheurer.com