High output catenary renewal trains (SRC), GEISMAR work trains responding to the industrialisation of catenary maintenance in France
High output renewal trains are well known in the track world for renewing rails, sleepers or ballast with high efficiency. Why not replicate this approach for catenary work? This is the specification that has been proposed in France by SNCF Réseau to renew almost 16,000 km of electrified track. After long months of design and manufacture in cooperation with Colas Rail and TSO Catenaries, the first GEISMAR SRC fast catenary suite is at work every night on the 25,000-volt network. In 2021, a second rapid catenary suite will operate on the 1,500-volt network. Unrivalled performance in catenary renewal has already been achieved.
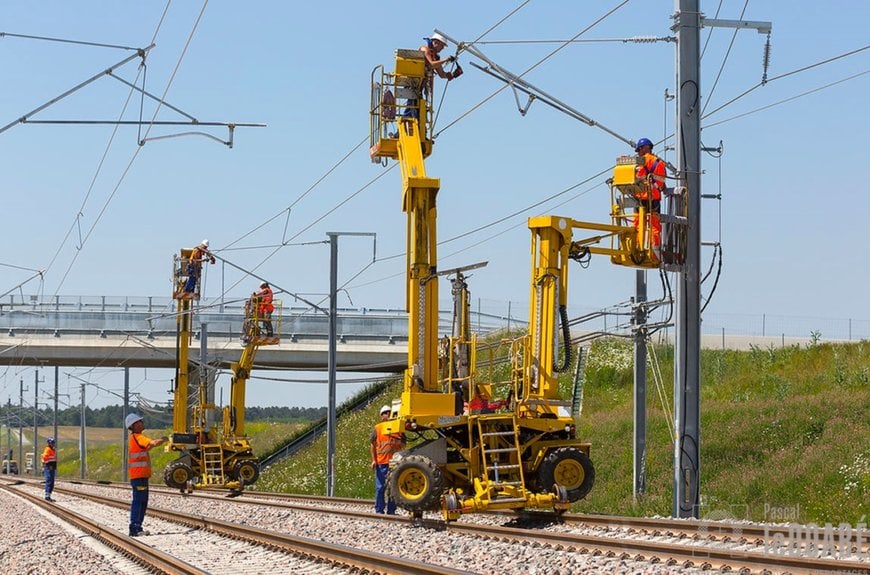
Catenary construction site with VCP road-rail vehicles
What is the situation of the catenary network in France?
France has nearly 30,000 km of railroads, half of which are electrified, which must be regularly maintained to ensure the safety and continuity of rail traffic. This electrified network is 65% divided into 25,000 VAC (volts in alternating current) and 35% of the network into 1,500 VDC (volts in direct current).
– Supports 25 kV – Supports 1 500 V
In addition to the renewal of the catenary wires carried out with rolling and unrolling trains, SNCF studies have shown that it is also essential to replace the support on the 25,000 VAC catenary and the entire pole and support on the 1,500 VDC catenary. The 1,500 VDC catenary is generally older, with some sections of track having poles that are almost 100 years old! Given the density of the electrified network in France, new high-performance trains were needed to complete this work within a suitable timeframe. It was in this context that the High Output Catenary Renewal Trains appeared.
What new challenges does the renewal of the catenary impose?
- In order to renew these two types of catenary (1,500 VDC and 25,000 VAC), logistical resources are generally heavy to implement:
- new catenary equipment delivery in the area;
- numerous road-rail vehicles to be organised and set up;
- different catenary equipment;
- preparatory work prior to the replacement work;
- work difficult to make safe with rail traffic on the adjacent track;
- significant mobilisation of human resources.
With traditional means, it takes on average about 30 minutes to replace a catenary support. In cooperation with Colas Rail and TSO Catenaries, GEISMAR has taken up the challenge of dividing this replacement time by 3 in order to speed up the replacement rate of the supports that need it most. This was a small revolution in the railway world because it was necessary to find ways of breaking down and industrialising catenary work with trains, known as High Output Catenary Renewal Trains (SRC). Among the difficulties encountered, the catenary lines are almost never the same. Indeed, multiple configurations or types of poles and supports have been installed over the years.
What are the objectives to be achieved by the High Output Catenary Renewal Trains?
The maintenance objectives for each night’s work are:
FOR THE CATENARY 25,000 VAC:
- the renewal of 24 supports (a) and the associated droppers (b);
- the replacement of 2 tensioning devices (c) and 2 counterweights (d);
- the replacement of the connections and bracket anchoring;
- the maintenance of the contact (e) and messenger (f) wires during the replacement of the tensioning devices and counterweights.
FOR THE 1,500 VDC CATENARY:
- the replacement of 15 poles;
- renewal of the anchoring points on the existing foundations;
- the renewal of an anchor (tensioning device and counterweight).
In order to avoid having to completely reposition the droppers, thus creating additional operations and costs, the new posts must be in the same place as the old ones. A first preparatory train will pass before the replacement train in order to place threaded rods in the existing concrete blocks at the foot of the poles.
Installation of the new poles with a winch on the threaded rods embedded in the concrete cubes
What are the High Output Catenary Renewal Trains made up of to achieve their objectives?
In collaboration with end users, GEISMAR has designed and produced two trains:
The 25,000 VAC train, operated since 2019 by Colas Rail, is consisting of:
- wagons with a self-propelled cradle with trailer (1);
- a crane wagon for depositing used supports with a hydraulic clamp (2);
- a work wagon consisting of the catenary wire retaining mast (3);
- a crane wagon for installing new supports with hydraulic clamp from new console racks (4);
- temporary track wagons consisting of a self-propelled cradle for catenary measurement (5).
The 1,500 VDC train, operated in 2021 by TSO Catenaries, is consisting of:
- temporary track wagons with crane runway where the gantries with beams and clamps (2) are located, allowing the used poles to be evacuated onto storage trays (1);
- a crane wagon for depositing the used poles with a winch and new console racks (3);
- a working wagon where the poles are held by a hydraulic clamp, cut and then removed with a crane (4);
- a crane wagon for placing the new poles with a winch (5);
- temporary track wagons integrating the gantry cranes with beams (6) allowing the new poles to be transported (7).
Every night, the 25,000 VAC High Output Catenary Renewal Train is at work and gives satisfaction. With the support of the GEISMAR teams, Colas Rail operators are gaining experience in adjusting equipment (cradles, cranes, masts, clamps, gantries, etc.) to synchronise their movements and save time on site.
SRC 25,000 VAC Train
Congratulations to the teams of GEISMAR Alsace, Rhône and Provence for their respective know-how in the design and manufacture of wagons, aerial platforms, cranes and gantries. Team spirit and pugnacity made it possible to successfully complete this unprecedented project!
We now hope that these French innovations can also be used to renew more efficiently the catenary of other networks outside Frances. The oldest networks, with a catenary configuration similar to France, will then be able to apply all the GEISMAR technology.
www.geismar.com