railway-international.com
15
'25
Written on Modified on
Proven Strategies for Effective Railcar Maintenance
Learn how tools like T-90 consist data and AAR-certified parts from Comet Industries can optimize your operations.
www.cometind.com
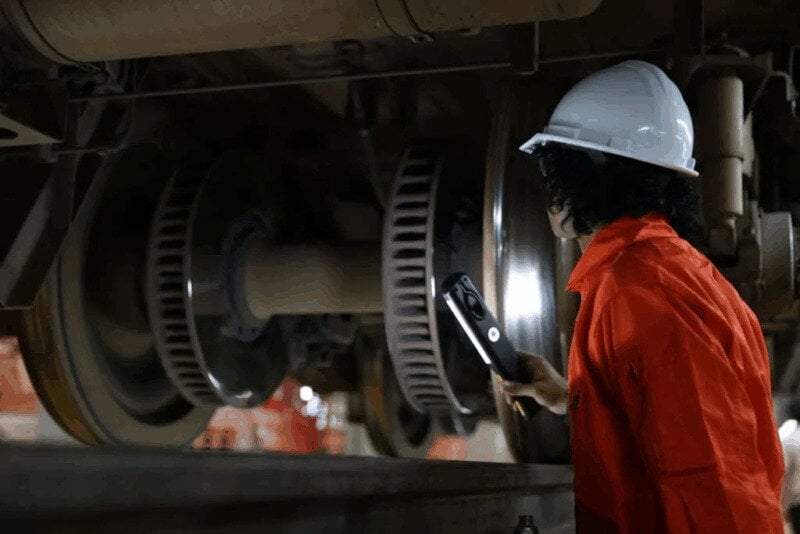
Effective railcar maintenance is at the heart of safe, efficient, and reliable railroad operations. From extending the life of components to minimizing costly downtime, a robust maintenance strategy can make all the difference. But with the complexity of railcar systems and the demands of modern-day logistics, maintenance managers are often left juggling multiple challenges.
We will explore proven strategies for railcar maintenance that can help railcar managers, fleet supervisors, and railroad professionals keep their operations running seamlessly. From understanding key components to leveraging advanced technology and certified parts, these actionable insights will elevate your maintenance practices.
The Importance of Railcar Maintenance
Every day, railcars move goods, raw materials, and products that fuel the global economy. Yet, the heavy loads and long distances they cover mean that wear and tear is inevitable. Adopting proactive maintenance is essential—not just for cost savings but also for ensuring safety and compliance with regulatory standards.
Effective railcar maintenance provides several key benefits:
. Prolongs Lifespan: Preventative maintenance helps avoid premature component failure.
. Improves Safety: Ensures essential components like brakes and couplers perform optimally.
. Reduces Downtime: Minimizes operational disruptions caused by unplanned repairs.
. Optimizes Costs: Extends the time between major overhauls and reduces the frequency of replacing expensive parts.
But where do we begin? It starts with understanding the key components of a railcar.
Understanding Key Railcar Components
Railcars consist of numerous interconnected systems, each requiring specific attention. Below are some of the most critical components to prioritize during maintenance checks:
. Suspension System: Includes bolsters, side frames, and springs that bear the railcar’s weight and ensure stability.
. Air Brake System: A crucial safety feature that efficiently regulates speed and brings the train to a controlled stop.
. Couplers and Draft Gears: Essential for connecting railcars while absorbing impact forces during operation.
. Wheelsets and Bearings: Critical for rolling performance and load distribution across the track.
Prioritizing regular inspections and servicing of these components is key to avoiding costly operational disruptions.
Common Railcar Maintenance Challenges
Railcar professionals often face hurdles when maintaining large fleets, including:
. Component Wear: Intensive usage wears out parts like yokes, brake beams, and hand brakes more frequently than anticipated.
. Locating Lost Cars: Inefficient tracking systems can lead to logistical bottlenecks.
. Regulations Compliance: Meeting strict AAR (Association of American Railroads) standards requires rigorous adherence to protocols.
. Unplanned Downtime: Unexpected breakdowns can delay shipments and impact profitability.
Addressing these challenges head-on requires adopting innovative tools and reliable processes.
Comet AEI Systems: A 30-Year Legacy in Rail Logistics
When discussing innovation in rail logistics, one name consistently stands out—Comet Industries. For over 30 years, Comet has been the backbone of rail operations across North America. Their RailNET AEI systems bring unmatched accuracy and reliability to Automated Equipment Identification (AEI), powering nearly 5,000 sites across the continent.
With Comet’s AEI systems, railcar maintenance managers can:
. Track and locate cars faster.
. Rely on actionable T-90 consist data for strategic decision-making across operations.
. Monitor railcar health using wayside systems for early issue detection.
Comet’s solutions offer companies a way to stay ahead in the dynamic world of railroad logistics.
Leveraging T-90 Consist Data for Enhanced Operations
T-90 consist data is another game-changer for railcar managers. By analyzing data captured from AEI systems, you can:
. Improve Shipment Accuracy: Avoid logistical errors in transit.
. Optimize Fleet Movement: Ensure cars are utilized efficiently and aren’t sitting idle.
. Plan Predictive Maintenance: Use insights for early detection of potential failures.
This data isn’t just numbers—it’s actionable insights that help streamline operations and enhance fleet performance.
Preventative Maintenance Strategies
Preventative maintenance is a proactive approach that saves time, money, and stress. Here’s how to implement it effectively:
1 . Establish Maintenance Schedules: Create a calendar of regular inspections and service checks.
2 . Train Your Team: Provide technicians and staff with up-to-date knowledge of railcar systems and lifecycles.
3 . Plan for Seasonal Adjustments: Harsh winters or hot summers take a toll on parts, so plan accordingly.
4 . Document Everything: Maintaining logs helps track long-term performance and prepare for audits.
5 . Leverage Predictive Technologies: Use data analytics tools to identify and rectify minor issues before they escalate into major problems.
Using AAR Certified Parts and Services: Ensuring Quality and Compliance
Using quality parts is just as critical as scheduling maintenance. AAR-certified parts meet the highest regulatory standards required across the industry, ensuring reliability and safety.
Comet Industries offers a robust inventory of AAR-certified railcar components, including:
. Bolsters and Side Frames
. Draft Gears and Couplers
. Brake Beams and Hand Brakes
Their Kansas City yard, with over 7 acres of inventory, ensures rapid delivery of high-quality freight car and locomotive parts.
Outsourcing your reconditioning needs to an AAR-certified repair facility also ensures compliance with M-214 standards while maintaining the durability of essential components.
The Role of Technology in Modern Railcar Maintenance
Technology continues to reshape railcar maintenance. The following tech advancements should be part of your strategy:
. Automated Condition Monitoring Systems: Instantly flag underperforming components, reducing manual interventions.
. Mobile Apps for Technicians: Provide remote access to maintenance logs, manuals, and checklists.
These technologies ensure maximum efficiency, safety, and cost savings for rail operations.
Case Studies: Successful Railcar Maintenance Programs
To understand the impact of these strategies, consider these examples:
. Company A integrated Comet’s AEI systems into their tracking process, reducing fleet downtimes by 15%.
. Fleet Operator B implemented predictive analytics and extended component replacement cycles, saving $500,000 annually.
. Logistics Firm C switched to AAR-certified brake beams and reduced brake-related failures by 25%.
These examples highlight how adopting modern maintenance practices and tools directly improves safety and bottom-line performance.
Prioritize Safety, Efficiency, and Longevity in Rail Operations
Effective railcar maintenance isn’t just about compliance; it’s an investment in longevity and operational success. By understanding key railcar systems, leveraging T-90 consist data, and using certified parts, you can ensure smooth and efficient operations.
Looking for reliable railcar parts or advanced monitoring systems? Consider partnering with trusted providers like Comet Industries, whose legacy in rail logistics speaks for itself.
If you’re ready to optimize your railcar maintenance strategy, start exploring innovative tools and certified solutions today. A safer, more efficient rail future is within reach.
The Importance of Railcar Maintenance
Every day, railcars move goods, raw materials, and products that fuel the global economy. Yet, the heavy loads and long distances they cover mean that wear and tear is inevitable. Adopting proactive maintenance is essential—not just for cost savings but also for ensuring safety and compliance with regulatory standards.
Effective railcar maintenance provides several key benefits:
. Prolongs Lifespan: Preventative maintenance helps avoid premature component failure.
. Improves Safety: Ensures essential components like brakes and couplers perform optimally.
. Reduces Downtime: Minimizes operational disruptions caused by unplanned repairs.
. Optimizes Costs: Extends the time between major overhauls and reduces the frequency of replacing expensive parts.
But where do we begin? It starts with understanding the key components of a railcar.
Understanding Key Railcar Components
Railcars consist of numerous interconnected systems, each requiring specific attention. Below are some of the most critical components to prioritize during maintenance checks:
. Suspension System: Includes bolsters, side frames, and springs that bear the railcar’s weight and ensure stability.
. Air Brake System: A crucial safety feature that efficiently regulates speed and brings the train to a controlled stop.
. Couplers and Draft Gears: Essential for connecting railcars while absorbing impact forces during operation.
. Wheelsets and Bearings: Critical for rolling performance and load distribution across the track.
Prioritizing regular inspections and servicing of these components is key to avoiding costly operational disruptions.
Common Railcar Maintenance Challenges
Railcar professionals often face hurdles when maintaining large fleets, including:
. Component Wear: Intensive usage wears out parts like yokes, brake beams, and hand brakes more frequently than anticipated.
. Locating Lost Cars: Inefficient tracking systems can lead to logistical bottlenecks.
. Regulations Compliance: Meeting strict AAR (Association of American Railroads) standards requires rigorous adherence to protocols.
. Unplanned Downtime: Unexpected breakdowns can delay shipments and impact profitability.
Addressing these challenges head-on requires adopting innovative tools and reliable processes.
Comet AEI Systems: A 30-Year Legacy in Rail Logistics
When discussing innovation in rail logistics, one name consistently stands out—Comet Industries. For over 30 years, Comet has been the backbone of rail operations across North America. Their RailNET AEI systems bring unmatched accuracy and reliability to Automated Equipment Identification (AEI), powering nearly 5,000 sites across the continent.
With Comet’s AEI systems, railcar maintenance managers can:
. Track and locate cars faster.
. Rely on actionable T-90 consist data for strategic decision-making across operations.
. Monitor railcar health using wayside systems for early issue detection.
Comet’s solutions offer companies a way to stay ahead in the dynamic world of railroad logistics.
Leveraging T-90 Consist Data for Enhanced Operations
T-90 consist data is another game-changer for railcar managers. By analyzing data captured from AEI systems, you can:
. Improve Shipment Accuracy: Avoid logistical errors in transit.
. Optimize Fleet Movement: Ensure cars are utilized efficiently and aren’t sitting idle.
. Plan Predictive Maintenance: Use insights for early detection of potential failures.
This data isn’t just numbers—it’s actionable insights that help streamline operations and enhance fleet performance.
Preventative Maintenance Strategies
Preventative maintenance is a proactive approach that saves time, money, and stress. Here’s how to implement it effectively:
1 . Establish Maintenance Schedules: Create a calendar of regular inspections and service checks.
2 . Train Your Team: Provide technicians and staff with up-to-date knowledge of railcar systems and lifecycles.
3 . Plan for Seasonal Adjustments: Harsh winters or hot summers take a toll on parts, so plan accordingly.
4 . Document Everything: Maintaining logs helps track long-term performance and prepare for audits.
5 . Leverage Predictive Technologies: Use data analytics tools to identify and rectify minor issues before they escalate into major problems.
Using AAR Certified Parts and Services: Ensuring Quality and Compliance
Using quality parts is just as critical as scheduling maintenance. AAR-certified parts meet the highest regulatory standards required across the industry, ensuring reliability and safety.
Comet Industries offers a robust inventory of AAR-certified railcar components, including:
. Bolsters and Side Frames
. Draft Gears and Couplers
. Brake Beams and Hand Brakes
Their Kansas City yard, with over 7 acres of inventory, ensures rapid delivery of high-quality freight car and locomotive parts.
Outsourcing your reconditioning needs to an AAR-certified repair facility also ensures compliance with M-214 standards while maintaining the durability of essential components.
The Role of Technology in Modern Railcar Maintenance
Technology continues to reshape railcar maintenance. The following tech advancements should be part of your strategy:
. Automated Condition Monitoring Systems: Instantly flag underperforming components, reducing manual interventions.
. Mobile Apps for Technicians: Provide remote access to maintenance logs, manuals, and checklists.
These technologies ensure maximum efficiency, safety, and cost savings for rail operations.
Case Studies: Successful Railcar Maintenance Programs
To understand the impact of these strategies, consider these examples:
. Company A integrated Comet’s AEI systems into their tracking process, reducing fleet downtimes by 15%.
. Fleet Operator B implemented predictive analytics and extended component replacement cycles, saving $500,000 annually.
. Logistics Firm C switched to AAR-certified brake beams and reduced brake-related failures by 25%.
These examples highlight how adopting modern maintenance practices and tools directly improves safety and bottom-line performance.
Prioritize Safety, Efficiency, and Longevity in Rail Operations
Effective railcar maintenance isn’t just about compliance; it’s an investment in longevity and operational success. By understanding key railcar systems, leveraging T-90 consist data, and using certified parts, you can ensure smooth and efficient operations.
Looking for reliable railcar parts or advanced monitoring systems? Consider partnering with trusted providers like Comet Industries, whose legacy in rail logistics speaks for itself.
If you’re ready to optimize your railcar maintenance strategy, start exploring innovative tools and certified solutions today. A safer, more efficient rail future is within reach.
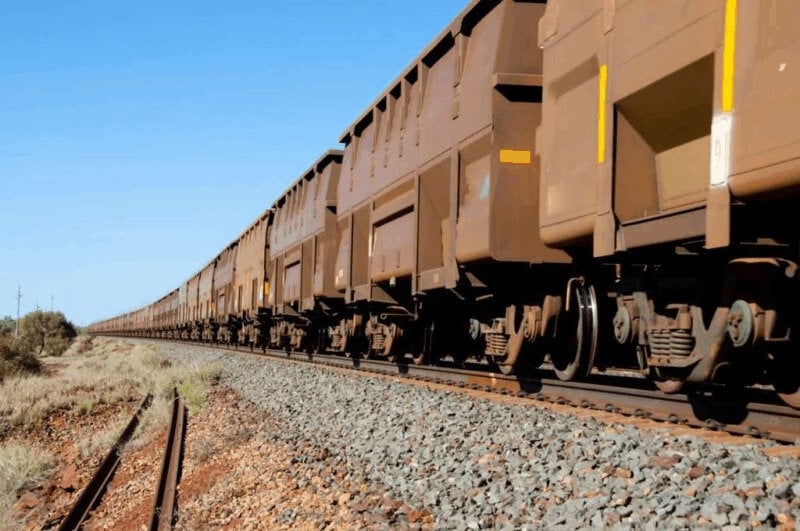
FAQs
Q: What is railcar maintenance, and why is it important?
A: Railcar maintenance involves the regular inspection, service, and repair of railcars to ensure they operate safely and efficiently. It is crucial because railcars endure extensive wear and tear from transporting heavy loads and travelling long distances. Proper maintenance extends the lifespan of components, enhances safety, reduces downtime, and ensures compliance with regulatory standards.
Q: What are the key components to prioritise during railcar maintenance?
A: Critical railcar components include the suspension system (bolsters, side frames, and springs), air brake system, couplers and draft gears, and wheelsets and bearings. Regular inspections and servicing of these parts help prevent costly breakdowns and ensure smooth operations.
Q: What are the biggest challenges in maintaining railcars?
A: Some common challenges include frequent component wear, difficulty in tracking lost cars, meeting regulatory compliance with AAR standards, and unplanned downtime due to unexpected failures. Addressing these requires adopting proactive maintenance strategies and leveraging innovative tools like tracking systems and automated monitoring.
Q: How does preventative maintenance benefit railcar operations?
A: Preventative maintenance involves scheduling regular inspections, training staff, and using predictive analytics to identify potential issues before they escalate. This approach saves time, reduces repair costs, minimises downtime, and ensures components last longer while maintaining safety and compliance.
Q: What role does technology play in modern railcar maintenance?
A: Technology has transformed railcar maintenance with tools like automated condition monitoring systems that instantly flag underperforming components and mobile apps that provide technicians with remote access to maintenance logs and manuals. These advancements increase safety, boost efficiency, and lower operational costs.
Q: How can T-90 consist data improve railcar operations?
A: T-90 consist data provides actionable insights by improving shipment accuracy, optimising fleet utilisation, and enabling predictive maintenance. By analysing this data, railcar managers can reduce errors, better allocate resources, and prevent equipment failures.
Q: Why are AAR-certified parts important in railcar maintenance?
A: AAR-certified parts meet stringent industry standards, ensuring reliability, safety, and compliance. Using certified parts, such as those offered by trusted providers like Comet Industries, reduces the risk of equipment failure and helps maintain the quality of railcar systems.
Q: What are some strategies to enhance efficiency in railcar maintenance?
A: To improve efficiency, managers should establish maintenance schedules, document all servicing activities, train personnel on railcar systems, and adopt advanced technologies like predictive analytics and automated monitoring systems. Outsourcing to AAR-certified repair facilities for reconditioning can also ensure quality and compliance.
Q: What is Comet Industries, and how can it support railcar maintenance?
A: Comet Industries is a leading name in rail logistics with over 30 years of experience. Their RailNET AEI systems enhance car tracking accuracy, while their extensive inventory of AAR-certified parts ensures reliable component replacements. With solutions like T-90 consist data analytics and wayside monitoring systems, Comet helps railcar managers optimise operations.
Q: Can you share examples of successful railcar maintenance strategies?
A: Several companies have successfully improved operations by adopting modern maintenance strategies. For instance, some have integrated Comet AEI systems to reduce downtime by 15%, while others have used predictive analytics to save hundreds of thousands annually. Switching to AAR-certified parts has also significantly decreased component failure rates. These case studies illustrate the tangible benefits of leveraging innovative tools and approaches.
www.cometind.com