railway-international.com
11
'24
Written on Modified on
High-accuracy ASC sensors ensure safe and comfortable train operation
The smart sensor systems ASC AiSys enable real-time monitoring of the assets and early detection of damages.
www.asc-sensors.de
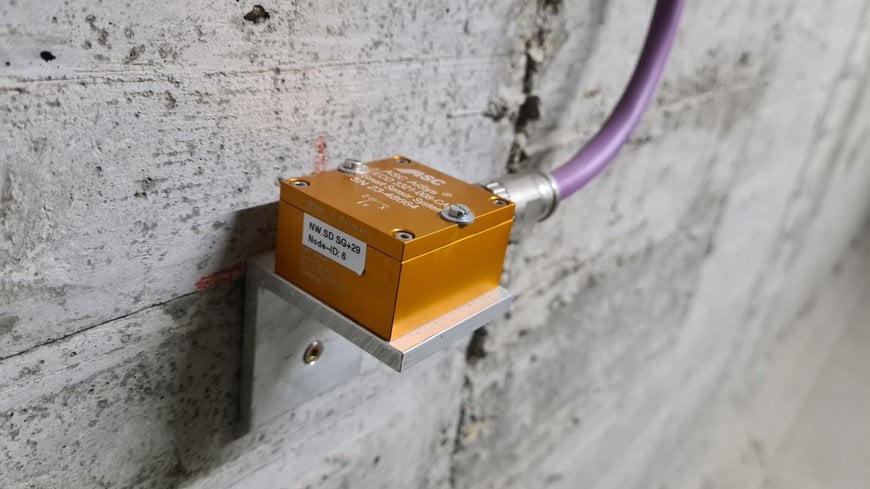
Without inertial sensors, modern rail transport would be inconceivable. They detect the position of trains, monitor the state of the tracks, and ensure optimal travel comfort. The smart sensor systems ASC AiSys® enable real-time monitoring of the assets and early detection of damages, so that infrastructure operators can plan their maintenance activities even more efficiently in the future.
Inertial sensors perform numerous important tasks in the development and operation of trains. One of them is high-precision measurement of oscillations and vibrations on rolling stock, tracks, and bridges. The data obtained from these measurements form the basis for safe, comfortable rail transport. Engineers can draw valuable information from them for train design and infrastructure maintenance. Sensors also ensure that the train dispatchers at the Deutsche Bahn railway control centers always know the exact location of any given train. Satellite navigation alone is not enough, because the signals are susceptible to interference.
ASC is specialized in measurement technology and manufactures a wide range of highly accurate accelerometers and gyroscopes, as well as Inertial Measurement Units (IMU) for rail transport testing and monitoring. The sensors collect data in a wide variety of applications – not only in rolling stock, but also on tracks or bridges.
ASC Is a Partner in the DRS Alliance
Leading European rail technology companies joined forces in October 2021 to form the Digital Railway Solutions (DRS) Alliance, with the aim of increasing the efficiency, safety, and performance of the world’s railway networks by means of digital technologies. DRS aims to develop sustainable and efficient solutions for network operators and transport companies in Europe. ASC is one of the founding members of DRS and will bring to the alliance its complete product portfolio in analog, digital, and smart form.
With its ASC AiSys® smart sensor systems, ASC can unlock the solutions to the future challenges in rail transport. These systems can be used for any acceleration, vibration or angular velocity measurement applications and are designed according to the customer’s requirements. The main difference between them and analog and digital sensors is that the smart sensor systems process and evaluate the acquired measurement data and extract predefined feature vectors. This involves, for example, the implementation of algorithms to calculate velocity and displacement based on acceleration.
Smart sensor systems can be integrated as an open system into any other systems. They are therefore the basis for numerous monitoring solutions for vehicles and infrastructure, AI applications, intelligent sensor networks, or Industry 4.0 applications. They can be used for realtime monitoring solutions, e.g. for rail vehicles or rail infrastructure, but also for detecting derailments.
Fatigue Strength Testing Under Extreme Conditions
Capacitive accelerometers from ASC do many things, including making trains safer. Alstom, a rolling stock manufacturer, uses them for example to determine running dynamics (according to EN 14363) and bogie strength (according to EN 13749) under real-life conditions. The ASC sensors used for this purpose not only have a high signal amplitude of ±2.7 V for measurement ranges from ±2 g to 200 g, but also a wide frequency response range from DC up to 7 kHz. They also have high long-term stability, enabling accurate measurement of even lowest linear acceleration amplitudes and low-frequency, dynamic accelerations. The sensors are extremely robust to weather conditions, can withstand intense shocks of up to 6,000 g, and operate in a temperature range between -40°C (-40°F) and +125°C (257°F). These are important prerequisites for use on test tracks, as the measurement technology is exposed to all kinds of weather on them.
Bridging Navigation for Interrupted GNSS Signals
Sensors also play an important role in the exact positioning of trains, since knowing exactly where trains are is vital for rail safety. Satellite navigation alone is not enough, as GNSS signals are lost in tunnels, forest areas or covered railway stations, with no or only very weak reception. Inertial Measurement Units from ASC take over position determination in these areas, thus bridging the time taken for the satellite signal to be fully available again. IMUs are ideal for this field of application because they capture even the slightest angular velocities and linear movements as well as are based on a very compact and flexible design.
Track Damage Detected Early
Capacitive and piezoelectric accelerometers are also essential for continuous track monitoring (CTM), as are gyroscopes. Deutsche Bahn AG has been using ASC sensors on its long-distance trains for several years, with the sensors in normal operation measuring the acceleration in the wheel set bearings and the acceleration inside the car bodies (according to EN 13848).
DB Systemtechnik GmbH – Deutsche Bahn’s engineering office – can use the data obtained to identify irregularities in the track geometry. Variations in longitudinal level have a major impact on performance levels. If there are errors in the geometry, maintenance measures must be taken immediately, in order to avoid speed restrictions or, in extreme cases, track section closures. Continuous track monitoring using sensors and sensor systems allows potential damage to be detected and remedied at an early stage.
No Efficiency Improvements Without Digitization
Analog sensor technologies are mainly deployed in the field of testing and measurement, whereby detailed characterizations of vehicles and infrastructure can be made on a temporary basis, usually under known boundary conditions. The volume of rail passengers is, however, constantly on the increase, and this in turn leads to an increasing load on the railway network and the trains. Digital technologies are increasingly used in the rail sector to meet the high demands.
ASC’s digital sensors of the ASC DiSens® series work with the highest levels of precision and can transmit their signals without interference over great distances. This means that digital sensors are particularly suitable for monitoring infrastructures, such as bridges and buildings, where extremely long cables are used. Furthermore, in railway applications in particular, shocks of up to 400 g can be expected. This can lead to saturation of the the analog output signal, which in turn affects data processing because valuable measurement data is clipped or waveforms are deformed. The ASC DiSens® ECO accelerometers therefore have already implemented filter settings, to adapt sampling rate and cut-off frequency to the respective measurement task. Faulty measurements during test drives can thus be significantly reduced. They also offer another advantage: Since the analog input signals are already converted into digital output signals in the sensor, classic data acquisition is not necessary. Instead, the data can usually be processed directly on the measurement PC. ASC DiSens® sensors are available with digital interfaces such as RS-232 and CAN.
What Turns a Digital Sensor into a Smart Sensor System?
Analog measurement technology and experience from many applications are the basis for the implementation of the ASC AiSys® smart sensor systems. The modular system is based on proven and tested hardware components, and therefore on reliable sensor elements for determining the physical values of acceleration and/or angular velocity, the housing suited to the harsh environment conditions and the cable assembly. Also additional electronics for analog-to-digital conversion and standardized interfaces are integrated. The main feature of the sensor systems is, however, their capacity to analyze the collected data and extract predefined feature vectors. ASC AiSys® smart sensor systems provide the information, while the user takes care of determining which information is visualized and required for the appropriate end users. The user is always responsible for the data sovereignty and application programming interfaces (APIs) are used to implement customer-specific algorithms.
ASC also develops algorithms that allow velocity and displacement to be calculated on the ASC AiSys® smart sensor system. This has already been successfully implemented in a project to develop a sensor-based smart monitoring system for wind turbines. The aim was to calculate the wind tower deflection from the measured accelerations in order to determine types of wear and aging processes. In addition to the double numerical integration, the static offset components and drift-dependent components had to be compensated for by means of frequency analyses. All calculation steps for this were carried out comprehensively on the smart sensor system and these can be adapted for specific applications.
ASC AiSys® Smart Sensor Systems Transmit Data in Real Time
Previously, data used to be recorded externally and evaluated periodically. With the new ASC AiSys® smart sensors, processing is done directly on the sensor, which then issues a status message using the traffic light principle. Rail asset owner can now monitor the condition of rolling stock and infrastructure in real time and detect irregularities even more quickly. This keeps the number of service interruptions down to a minimum.
Interruption-free operation is indeed the basic prerequisite for more intensive utilization of railway lines. Deutsche Bahn’s overarching “Strong Rail” strategy is aimed at helping achieve the German government’s transport and climate policy objectives. ASC sensors can therefore indirectly contribute to the transfer of traffic from road to rail.
www.asc-sensors.de