railway-international.com
19
'24
Written on Modified on
HITACHI DEVELOPS WORLD'S FIRST COMMERCIAL COPPER DIE-CAST ROTOR FOR RAILWAY TRACTION MOTORS
The technology aims to achieve both efficiency and lightweight in traction motors, contributing to carbon neutrality.
www.hitachi.com
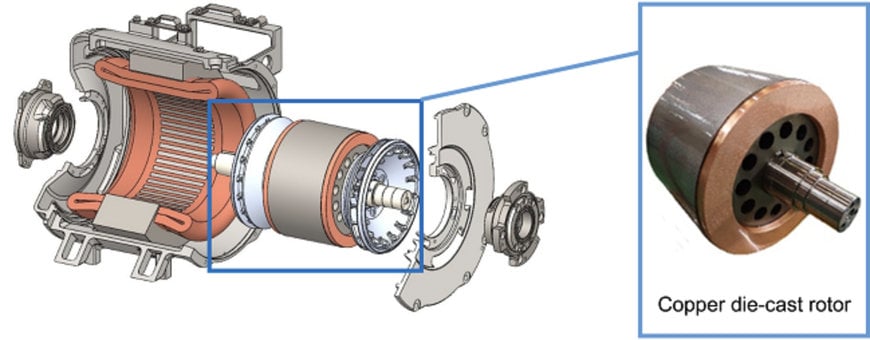
Internal structure of traction motor with copper die-cast rotor
Hitachi Industrial Products has commercialized the world's first copper die-cast rotor for railway traction motors as lightweight rotors. By adding weight-reduction technology to the high-efficiency technologies that Hitachi Industrial Products already possesses, we will contribute to further energy savings and reduced environmental impact of railway vehicle operation.
To further reduce the weight of rotors, a component of traction motors, Hitachi Industrial Products has developed a copper die-cast rotor for railway traction motors.
The copper die-cast rotor is manufactured by die-casting copper, a conductor, and is approximately 15 kg lighter in weight than conventional rotors in which copper bars and end rings are brazed together ("copper bar type"). Going forward, this new rotor will be applied to railway projects.
Hitachi Industrial Products' conventional lineup of traction motor rotors consists of two types: the copper bar type, which is constructed by inserting a rod-shaped copper bar into a slot in the iron core, and the aluminium die-casting type, which is manufactured by die-casting an aluminium conductor.
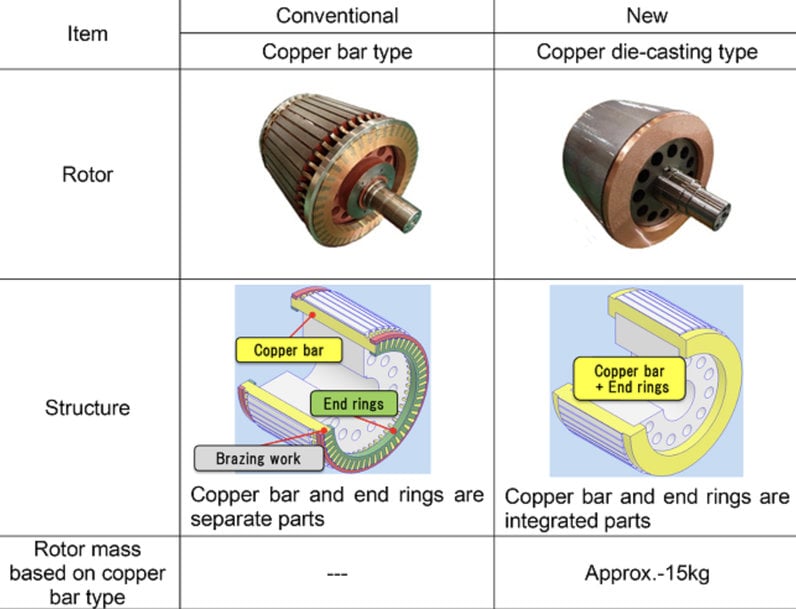
In order to contribute to the realization of a carbon-neutral society, we are promoting the improvement of the efficiency of traction motors. For our highly efficient products, we use copper bar-type rotor conductors made of copper material, which has lower losses than aluminium. To achieve both efficiency and weight reduction, we considered adopting the copper die-casting, and could reduce the number of parts by simplifying the structure while maintaining the efficiency achieved by using copper material. However, because the melting point of copper (approximately 1086°C) is higher than that of aluminium (approximately 660°C), the temperature of the molten copper becomes very high, making it extremely difficult to cast with good quality. In addition, because the rotor is intended for traction motors for railway, die-casting into larger rotors is necessary, which was an issue.
By applying the aluminium die-casting technology it has cultivated to copper, repeatedly prototyping and verifying copper die-cast rotors over several years, Hitachi Industrial Products established suitable design and verification methods for railway vehicle traction motors, developed and commercialized high-quality copper die-cast rotors.
The copper die-cast rotor will be exhibited at the International Railway Technology Trade Fair - InnoTrans 2024, which will be held in Berlin, Germany from Tuesday, September 24th to Friday, September 27th, 2024.
www.hitachi.com
Hitachi Industrial Products has commercialized the world's first copper die-cast rotor for railway traction motors as lightweight rotors. By adding weight-reduction technology to the high-efficiency technologies that Hitachi Industrial Products already possesses, we will contribute to further energy savings and reduced environmental impact of railway vehicle operation.
To further reduce the weight of rotors, a component of traction motors, Hitachi Industrial Products has developed a copper die-cast rotor for railway traction motors.
The copper die-cast rotor is manufactured by die-casting copper, a conductor, and is approximately 15 kg lighter in weight than conventional rotors in which copper bars and end rings are brazed together ("copper bar type"). Going forward, this new rotor will be applied to railway projects.
Hitachi Industrial Products' conventional lineup of traction motor rotors consists of two types: the copper bar type, which is constructed by inserting a rod-shaped copper bar into a slot in the iron core, and the aluminium die-casting type, which is manufactured by die-casting an aluminium conductor.
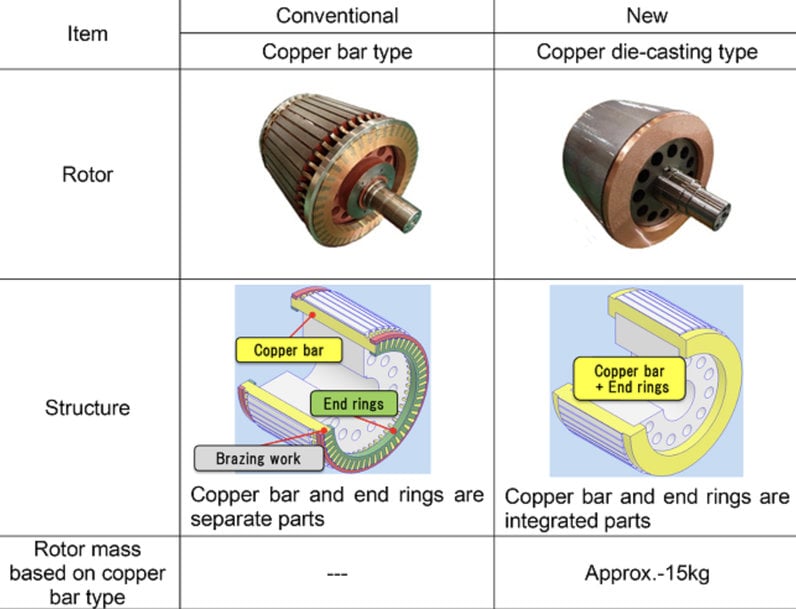
In order to contribute to the realization of a carbon-neutral society, we are promoting the improvement of the efficiency of traction motors. For our highly efficient products, we use copper bar-type rotor conductors made of copper material, which has lower losses than aluminium. To achieve both efficiency and weight reduction, we considered adopting the copper die-casting, and could reduce the number of parts by simplifying the structure while maintaining the efficiency achieved by using copper material. However, because the melting point of copper (approximately 1086°C) is higher than that of aluminium (approximately 660°C), the temperature of the molten copper becomes very high, making it extremely difficult to cast with good quality. In addition, because the rotor is intended for traction motors for railway, die-casting into larger rotors is necessary, which was an issue.
By applying the aluminium die-casting technology it has cultivated to copper, repeatedly prototyping and verifying copper die-cast rotors over several years, Hitachi Industrial Products established suitable design and verification methods for railway vehicle traction motors, developed and commercialized high-quality copper die-cast rotors.
The copper die-cast rotor will be exhibited at the International Railway Technology Trade Fair - InnoTrans 2024, which will be held in Berlin, Germany from Tuesday, September 24th to Friday, September 27th, 2024.