New milling tool for comprehensively machining grooved rails
Rheinbahn AG was looking for an innovative solution for the corrective maintenance of its grooved rails, and Vossloh developed a customized milling tool specifically designed for the purpose.
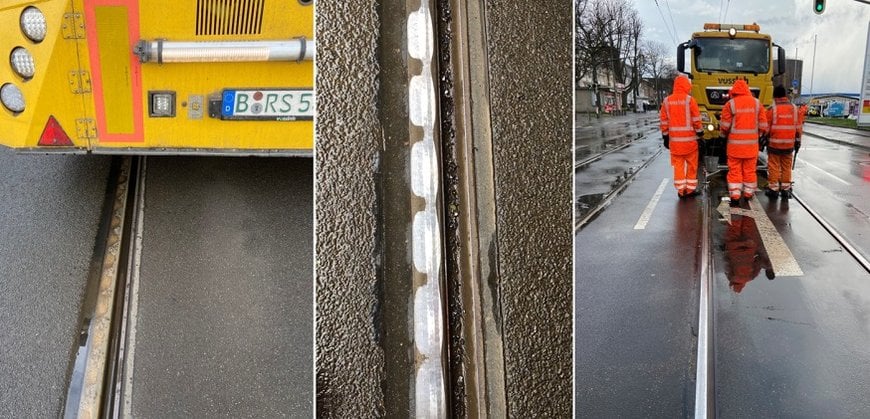
The tool was used on the Düsseldorf-based, light rail operator’s network in the spring, fulfilling the customer’s two requirements:
- No removal of the sealing compound in the gap along the rail’s outside edge
- Make highly effective use of the short period at night when the trains aren’t running in order to be able to machine all the line sections in question.
A concerted milling campaign was carried out at Rheinbahn in mid-March in order to sustainably reduce noise emissions on line sections with particularly heavy traffic. Laboriously removing the sealing compound and then replacing it with new sealant was not the customer’s preferred option, so Vossloh designed a customized milling tool based on the wheel profile of the vehicles used in Düsseldorf. With the combination of a positive-tangent cutting angle from the middle of the rail head and a cutting zone that extends over the inside edge of the milling wheel, the tool’s design meets the specified requirements. "Adding cutting tips to the wheel flange allows grooved rails to be fully machined, and that includes the bottom of the groove up to the gauge corner", explains the Technical Sales engineer responsible for the project, Steffen Riedel. "While the keyed-in cutting zone ensures that we only remove as much metal from the rail as necessary, cutting down an extra millimeter with larger removal rates guarantees that vehicles’ wheels will "spin freely"."
In order to make very effective use of the short track possessions during nightshifts, the road-rail milling truck was selected from Vossloh’s extensive pool of milling machines to do the work. With all the sealed asphalt surfaces in the area, the truck is guaranteed to be on site and ready to go when the shift starts. It can also access several track sections by road inside a single shift depending on the number of passes required.
"We found the quality and the focused, accommodating way the operating team works very convincing", acknowledged Peter Ahrens, Head of the Track Systems Department at Rheinbahn AG. "With corrective maintenance, we’re laying the ideal foundation for our systematic preventive maintenance approach." By combining the HSG-city that the operator has been using independently for some five years with occasional rail milling performed as a service order, the Düsseldorf-based network operator has the resources in place to carry out noise-mitigating rail maintenance.
www.vossloh.com