PTC 2.0: Wabtec Leads Step-Change Advances in Pivotal Rail Safety Software
Positive Train Control, or PTC, recently marked the four-year anniversary of its successful U.S. rollout.
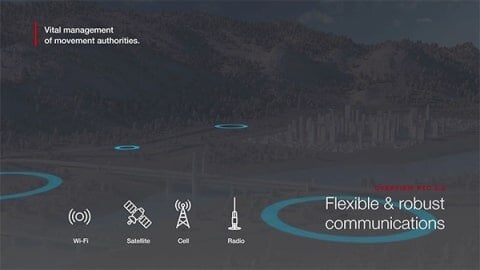
Yet this accomplishment, and the decade-plus development effort behind it, is rooted in a tragedy dating back to September 12, 2008, when a passenger train and freight train collided in the Chatsworth neighborhood of Los Angeles.
Following that terrible crash, Congress passed legislation requiring railroads to implement a national safety system that would monitor the movement of every train in the U.S., across nearly 60,000 miles of track, advising crews and automatically stopping a train as needed.
Operationalizing that mandate took 12 years and required massive investment and innovation among Class I railroads, smaller operators, and leading technology vendors, Wabtec included. To get a sense of the scale of this endeavor, consider what one Class I carrier told Los Angeles Times reporter David Lauter about complying: “BNSF had to build roughly 6,000 wayside towers to transmit signals along 11,500 miles of track and install onboard computers on 5,000 locomotives.” (Source: Los Angeles Times, “The U.S. finally has a system to prevent deadly rail accidents,” January 2, 2021.)
Lauter also noted another key – and exacting – requirement of PTC: “Because engines from one railroad frequently travel over tracks owned by another, the systems used by each of the country’s seven major freight railroads and more than two dozen smaller freight and commuter lines needed to be fully interoperable.”
What he didn’t know at the time is that the PTC software on BNSF’s 5,000 onboard computers (and the broader railroad industry’s 22,000+ onboard computers) would be developed by Wabtec, and that Wabtec’s PTC solution would become an industry standard, providing over 1 million miles of active train protection on revenue service every day, for 97 global rail operators.
A running start at PTC
Neither the railroad industry nor Wabtec were caught flat-footed by the landmark PTC legislation. Wabtec was already developing a safety product based on GPS and an on-board database populated with critical features for the route – and it had several pilot customers among the Class I carriers.
PTC solutions are built on four pillars. They are designed to protect trains from exceeding limits of authority; derailments due to excessive speed; passing through a switch that’s not lined for that train; and encroaching into work zones where workers and equipment might be operating.
Yet bringing all these capabilities to scale would pose a daunting challenge. Wabtec’s pilot PTC solution worked on only select sections of track, not the whole North American rail network. Much more ‘building out’ of the wayside signaling infrastructure and communications networks needed to be done, not to mention tackling the whole issue of interoperability.
PTC as ‘overlay’
With safety as its “north star,” and the four pillars of protection its first destinations, Wabtec pioneered PTC software innovation for the industry, notching several patents. However, it did so within the practical parameters of what the industry actually wanted.
“It’s important to understand that the rollout of PTC was shaped by the railroad industry’s desire to improve its operational playbook, not replace it,” offers Jeff Kernwein, Group Vice President, Digital Intelligence, Wabtec. “To that end, we designed our original PTC software to ‘look over the shoulder’ of the engineer to prevent mistakes, while preserving their autonomy to operate safely and perform their daily responsibilities.”
That ability to increase safety levels while respecting traditions earned Wabtec PTC software a home in every Class I carrier’s locomotive cab.
A new path forward for the rest of the world
Wabtec has been busy testing the limits of PTC software, with its latest version poised to rewrite conventional safety, capacity, and infrastructure-investment assumptions.
“Ten years ago, when we and the Class I carriers were in the thick of developing the first generation of PTC solutions, we were guided by the idea of PTC software acting as an overlay,” recalls Kernwein. “Today, we’re hearing from customers interested in exploring a new safety and capacity paradigm that requires less wayside infrastructure.”
For example, rather than relying on a signal-aspect or form-based authority, what if the authority could simply be conveyed to the railroad’s on-board PTC system without requiring wayside signals at all?
Such a shift could provide a compelling, lower-cost alternative to emerging rail networks around the world. Put another way, railroads in South America, Africa, South East Asia, and Australia could forego expensive wayside signaling buildouts and leapfrog directly to PTC 2.0, bringing their rail projects to life more quickly and economically – without sacrificing safety.
PTC 2.0: A best-case scenario for safety and capacity
In order to get to a world where wayside signals are no longer required and on-board solutions provide standalone authority for trains to move, the safety capabilities of new PTC systems must be further turbocharged.
Wabtec is providing a glimpse of this future in its PTC 2.0 offering, which contains the new “Independent Vital Office Controller” (IVOC) software that watches over the entire railroad. The IVOC knows every train’s location and characteristics, as well as where each train is allowed to go, enhanced by precision navigation.
“The combination of rules-based authority information and precision telemetry in PTC 2.0 stands to provide a step-change safety improvement while transforming the capacity planning function, allowing operators to fit more trains on their tracks safely, without having to default to ‘worst-case train’ spacing,” concludes Craig Green, Wabtec’s Senior Director overseeing the IVOC development.
‘Worst-case train’ scenario planning enhances line safety by ensuring track traffic is adequately spaced to accommodate worst-case scenarios, such as a heavy, coal-laden train traveling at top speed. This system safeguards trains by providing a large ‘just-in-case’ buffer between them.
However, with Wabtec’s PTC 2.0 solution, railroads can begin moving beyond ‘worst-case’ scenario planning to a new paradigm that safely maximizes capacity and profitability – all based on the ‘real-case’ locations and characteristics of each train on the block.
www.wabteccorp.com