railway-international.com
09
'20
Written on Modified on
The Growing Role of Additive Manufacturing in the Rail Industry: An Expert Talk
Global rail companies continue to face growing challenges to build and maintain trains faster and at lower costs. Striving for engineering and design excellence, strict material and functionality regulations in the rail industry add additional levels of complexity to producing new or spare rail parts. In order to meet industry requirements, Europe’s leading transport companies – Bombardier Transportation, Deutsche Bahn ESG and Siemens Mobility – have all invested in additive manufacturing technology. In this interview, experts from these companies each provide their insights into the rail industry’s inherent production challenges and how their adoption of additive manufacturing helps to address them.
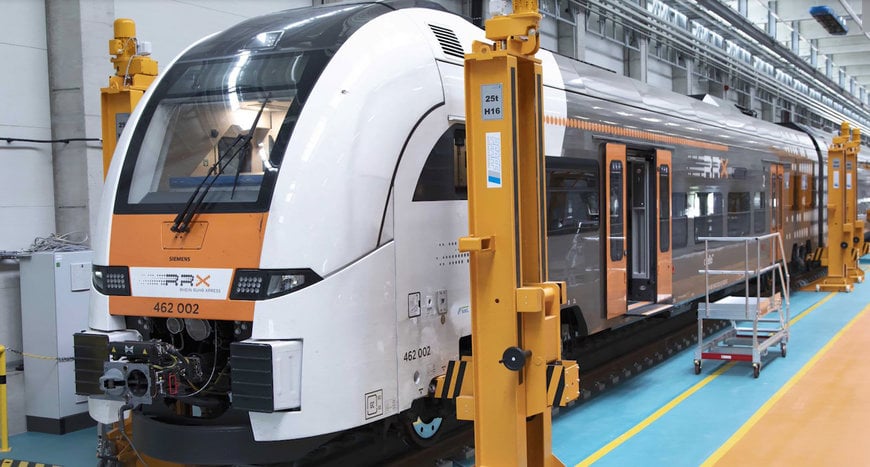
• AB: André Bialoscek, Head of Vehicle Physical Integration, Hennigsdorf – Bombardier Transportation
• MS: Martin Stevens, Mechanical Engineering Manager – Deutsche Bahn ESG
• MK: Michael Kuczmik, Head of Additive Manufacturing/Mobility Customer Services –Siemens Mobility
1. Can you explain the structure of the rail industry across the UK and Germany, in terms of the relationship between the operators, maintenance companies and rolling stock providers, as well as the role played by each?
MK: Across Germany, train operators handle the trains’ day-to-day operations and act as caretakers of public transportation. Maintenance companies ensure the availability and sometimes the attractiveness of the trains, while I would define rolling stock providers as suppliers of railroad vehicles and infrastructure to the owner – which could be the operators or a rental company. With reference to Siemens, we can fulfil each of these roles, so that we are able to support our customers with a complete portfolio, depending on the set-up and the demand.
AB: We operate in a similar way at Bombardier. Sometimes we are the sole rolling stock supplier, as well as being responsible for maintenance and the effective running of rail networks. It all depends on our customers’ business model.
MS: In the UK, it is somewhat fragmented. We have the rolling stock providers who finance the trains and lease them to the train operators. The train operators run the daily train services and undertake basic maintenance. Then we have maintenance and overhaul companies who deliver the large vehicle refurbishment and overhaul works, and finally we have engineering support companies such as DB ESG who deliver technical services to the industry.
2. Traditionally, what have been the biggest challenges in rail production?
MS: The biggest challenge across the board is very low production volumes. A large single train order of £800m would give you only 100 trains. That’s far too small a volume for typical mass production. Couple this with the fact that trains can operate for over 40 years and you end up with a situation where there are a huge number of different train designs that are still in operation, but only small quantities of each. This makes spare parts supply a challenge because you can’t use mass production techniques for any of these parts.
MK: I would echo the sentiment that low production volumes offer a significant challenge. In some cases, we have seen trains have a lifetime of up to 60 years. High one-off costs and sometimes very long lead times can result in obsolescence in the worst cases. Importantly, there is a significant challenge in the understanding and observance of regulations for specific use-cases and it is an absolute prerequisite. Therefore, you can only trust qualified suppliers.
AB: We need to deliver trains significantly faster than three to five years ago. This increases the general pressure on all facets of our operations, including engineering, procurement, manufacturing and testing/homologation. We’re constantly having to quickly adapt to the ever-changing market, and this can often mean challenging ourselves as a company to stay ahead of the curve. This is where additive manufacturing comes in.
3. Very interesting. So how does additive manufacturing play a role in overcoming these production challenges?
AB: Additive manufacturing is the right approach and a significant step forward for transport companies. Using additive manufacturing, we can rapidly produce physical parts in realistic dimensions throughout the design validation process for new train projects, not just prototypes – this includes series parts as well. Another important topic is on-demand servicing, in which additive manufacturing delivers huge advantages in replacing obsolete parts or manufacturing small batches, as well as re-engineering parts.
MK: Siemens Mobility is a long-standing adopter of the technology and has established a dedicated additive manufacturing team. This team of 18 supports our internal and external customers with engineering consultancy and support with the creation of spare parts using additive manufacturing. Our customers can order spare parts on demand via our Easy Spares Marketplace – depending on the required delivery time. If needed, we can re-work designs that are up to 30 years old, sometimes in conjunction with customers.
MS: Additive manufacturing is also a huge part of our business and is perfect for small production runs, as it enables straightforward design & print and eradicates upfront tooling costs or delays. For example, if five air vents were required for one small fleet of trains, this can only really be achieved with additive manufacturing. Although the individual unit cost will be higher, you can just buy 5 and receive in a couple of weeks, rather than buying 10,000 and getting them in 3 months. The huge positives far outweigh the minor negatives. In fact, we recently teamed up with Angel Trains, one of the big three UK rolling stock providers, and train operator Chiltern Railways, to deploy and successfully trial the first 3D printed parts on UK passenger trains.
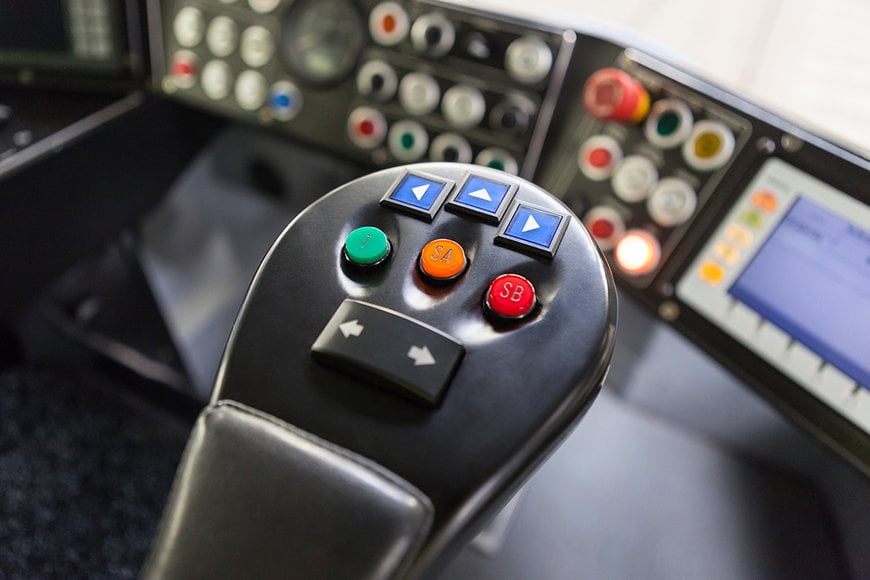
4. Martin, you mentioned air vents as an example of what you can produce using additive manufacturing technology. Are each of you able provide us with your own examples?
MS: We have several examples of parts on Chiltern Railways trains, such as interior grab handles. The original parts were cast aluminum and the design is now obsolete. Only rarely do these parts need replacing, but the operator was out of stock and if one breaks, it must be repaired within a week to meet regulations. Additive manufacturing is ideal in this situation – it allowed us to quickly produce five of these using Stratasys’ fire, toxicity and smoke compliant ULTEM 9085 resin material.
MK: In our case, we produce the front casing parts for light rail vehicles (also known as a streetcars), which is an after-sales use case. Streetcars share the track with other railway vehicles, and this is the root-cause of a lot of accidents. Our printed parts replace damaged sections such as the front skirt and will be delivered within days instead of months. Our customers can order one part instead of 10 and they don’t need to replace the entire front skirt, but only one third of it. This means that the work can be done by one person in a more time and cost-effective manner.
AB: Harking back to air vents, we were able to reduce production time for a customized air duct system part from four months to roughly four weeks using Stratasys additive manufacturing technology. That’s a resulting time saving of nearly 77 percent which is an incredible outcome for our department. A perfect example of our ability to now produce certain parts on-demand to our exacting needs without enduring lengthy production times or compromising on material quality.
5. This all sounds great, but is the certification of 3D printed parts an issue?
AB: With regards to the air duct system, the large part was 3D printed using our Stratasys F900 in ULTEM 9085 resin material, which significantly reduced the component’s weight and optimized overall material use. ULTEM 9085 resin importantly meets EN 45545-2 rail certification guidelines for smoke, toxicity and fire – a requirement for all train components produced at Bombardier Transportation.
MK: Typical certificates contain material properties like fire resistance and elongation at break, as well as part specific strength calculations. As the parts could be safety relevant, an update of the risk analysis for the whole system is often necessary. As such, we are also using ULTEM 9085 fire safety compliant material.
MS: I think we all agree that every part going onto a train needs some form of compliance assessment. Parts need to be proven compliant to the strict railway fire requirements and also prove strong enough to withstand a predefined load case.
6. For spare part production in the rail industry, what are your views on the business case for digital inventory?
MS: There are millions of pounds locked up in spares inventories for the UK fleets and a good proportion of these parts may never even be used. Moving to digital inventories for the simpler parts is certainly a move in the right direction.
MK: I would go one step further. It’s our belief that switching to virtual stock is essential moving forward – at least for corrective spare parts, where we do not know exactly if, when and how often they will be needed. Siemens Mobility already offers this via our Easy Sparovation concept. This comprises several possible options – standard ordering within the typical delivery times due to conventional production constraints, delivery within twenty-four hours in Europe from our stock, and printing on demand. The maintenance company or operator can decide based on how urgent the requirement is.
AB: Yes of course, it’s a big topic for us too. As additive manufacturing further expands into series production in the future and replaces more and more traditional rail parts, then we can really leverage the full potential of digital inventories.
7. There’s no doubt that additive manufacturing has been important for your businesses, but what future applications do you envisage?
AB: We expect to see new developments in additive manufacturing technology and materials come to market, which will be important in enabling us to further overcome production challenges in the rail industry. The ability to print even bigger parts would also be incredible, as I’m sure we would all agree.
MK: Absolutely – larger printed parts would be fantastic. For now, we will increase our use-cases together with our internal and external customers for spare parts, as well as for new vehicle designs. Also, we will proceed with the set-up of our worldwide printer network, including the interconnection of this network and our common MES (manufacturing execution system). This will enable us to improve time and cost efficiencies through more localized production.
MS: Looking ahead, our next step is to roll out what we have been doing for Chiltern Railways to the other 27 train operators in the UK. Together with Angel Trains, our aim in 2020 is to reverse engineer and supply two or three obsolete parts for each operator. This will be the most effective way of advertising the value of additive manufacturing to the rail sector.
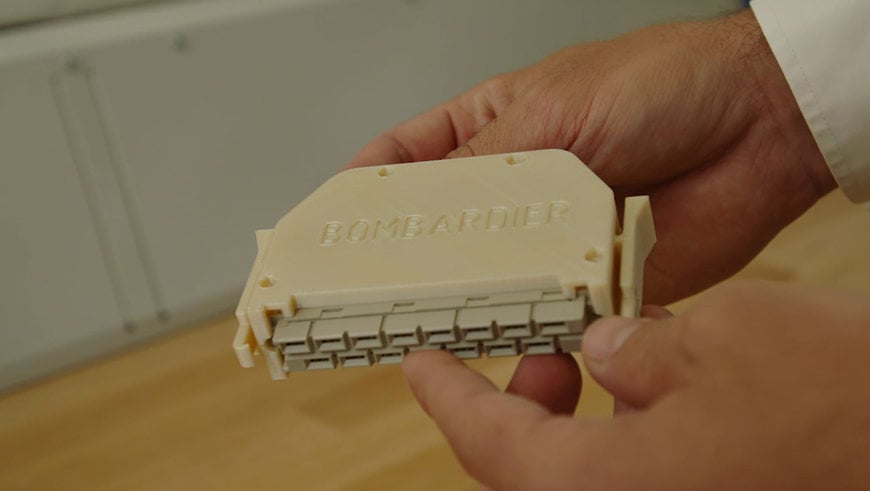
Pullout box: From the perspective of the 3D printing manufacturer, a few words from Yann Rageul, Director Manufacturing Solutions at Stratasys
The low volume benefits of additive manufacturing are a clear fit for the rail industry’s production requirements, therefore it’s no surprise that the technology has become an integral part of leading rail providers’ operations. Over the last three decades, additive manufacturing has matured and the range of possible applications has grown massively. 3D printing is now an industrial-grade tool that rail providers can leverage to secure their supplies of service parts, create tools that help maintenance and operations, and to enhance safety and customer experience.
As more and more rail companies optimize the use of additive manufacturing via digital inventory, producing spare parts on-demand, where they are needed and in the exact quantity required can be made a reality. Not only does this reduce the need for spare inventory and warehousing, but the speed at which trains can be maintained and repaired can be accelerated significantly. For those seeking to embrace this business model and get on board, the next stop is never too far away.
www.stratasys.com