Advanced Railway Signalling And Control Systems
The future of railway signalling lies in continued innovation, collaboration, and investment in cutting-edge solutions, says Milton D’Silva.
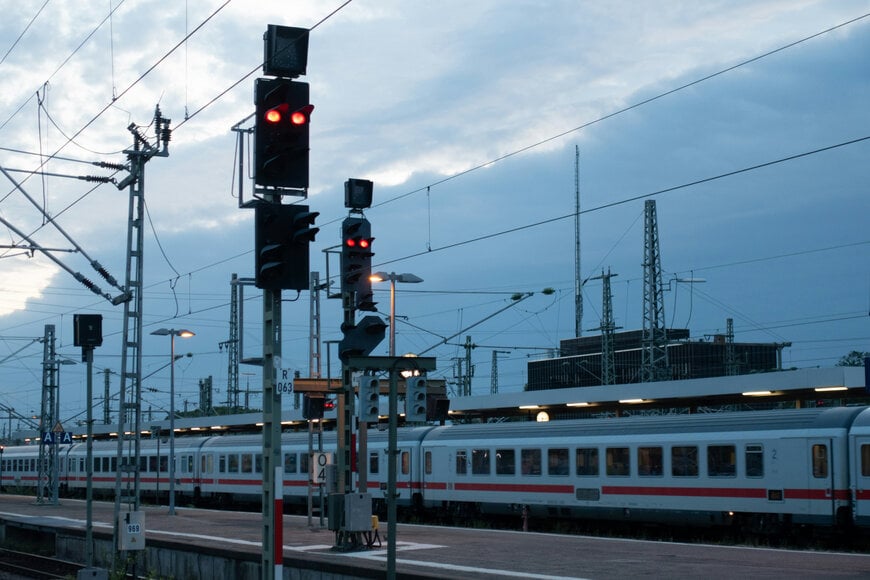
The Industrial Revolution of the late 18th century laid the foundation for modern railways by introducing two key elements: the steam engine and tracks. However, it was not until 1804 that the first steam-powered railway train ran at the Penydarren ironworks in South Wales, UK. The first regular passenger train service began in 1830, connecting Manchester and Liverpool. Around the same time, the United States was developing its own rail system, commonly referred to as a ‘railroad’.
Early railway signalling relied on simple methods such as hand signals, flags, lamps for nighttime use, and revolving boards. Since trains were few and operated on fixed schedules, these basic signalling techniques were sufficient. However, as railway traffic increased and trains became more frequent, this rudimentary system quickly proved inadequate, necessitating more advanced signalling solutions.
Effective railway signalling and control systems are crucial for safe and efficient train operations. These manage train movements, help prevent collisions, and optimise capacity on rail lines through features like automatic train protection, centralised control, and real-time communication, enhancing passenger safety and operational reliability.
The evolution of railway signalling systems
The history of railway signalling began with the opening of the Manchester-Liverpool railway in 1830, when hand signals were used initially, but soon was replaced by movable signals with the revolving board. One of the most interesting developments in the early days was the semaphore signals, patented in the early 1840s by Joseph James Stevens, which became the most widely used mechanical signal system. The semaphore signal basically used a pivoted arm to display different indications to train drivers by changing the angle of the arm. Semaphore signals were used widely until the early 20th century, and are still in use at a few places, with some modifications. As railways became a popular mode of transport and the network spread rapidly, the signalling systems also gradually evolved in stages, from the development of fixed lineside signals, followed by electric telegraphs and later, the interlocking mechanisms for points and signals. Power signalling appeared at the turn of the 20th century, and was followed by the development, first of electrical, and then electronic signalling systems. Today communication-based systems are more prevalent with digital interfaces.
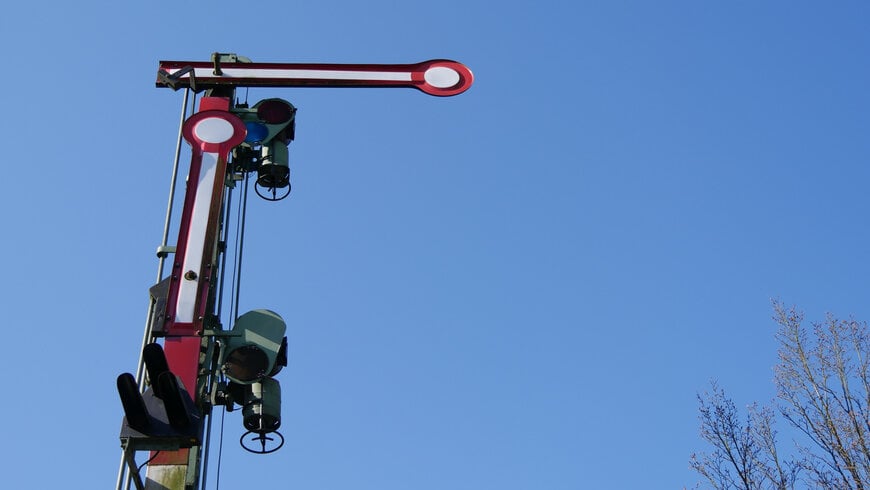
The semaphore signal basically used a pivoted arm. Image by Tabble from Pixabay
The evolution of railway signalling systems is thus a journey from basic mechanical controls to highly sophisticated digital automation, ensuring safer and more efficient train operations, as can be seen from the evolutionary stages described in the following paragraphs with the approximate timelines:
Early mechanical signalling (19th Century - Early 20th Century)
The earliest railway signalling systems were manual and mechanical, relying on human operators and physical signals to control train movements. The main developments during this period were:
- Time Interval System (Pre-1850s): Trains were spaced apart based on time intervals, relying on the operators' judgment. This method was unreliable and prone to accidents.
- Semaphore Signals (Mid-1800s - Early 1900s): Rotating arms were used to indicate whether a train should stop or proceed. These arms were controlled manually from trackside signal boxes.
- Fixed Block System (Late 19th Century): Tracks were divided into fixed sections (blocks), allowing only one train per block at a time to prevent collisions.
- Interlockings: These were introduced to ensure safe route settings by mechanically linking signals and switches.
The introduction of electricity and relays automated many railway operations, making signalling systems more reliable. Key advancements include:
- Track Circuits (1872 - Early 1900s): Allowed automatic train detection by sending electrical currents through rails. Signals could now be automatically cleared or set to danger based on train occupancy.
- Electromechanical & Relay Interlocking (Early 1900s - 1950s): Replaced mechanical interlocking with electrical relays, increasing efficiency. Allowed for centralised control over wider railway networks.
- Colour Light Signals (1920s - 1960s): Replaced semaphores with electric light signals, improving visibility. Enabled automated aspects like approach control, where signals adjusted based on train speed and track occupancy.
As computing power increased, railways adopted microprocessors and digital control to further automate and optimise train operations. Major innovations during this period:
- Solid-State Interlocking (SSI) (1980s - Present): Used microprocessors instead of relays, allowing more complex, fail-safe signal control.
- Cab Signalling (1970s - 2000s): Train drivers received speed and movement instructions directly in the driver’s cab, reducing reliance on trackside signals.
- Automatic Train Protection (ATP) (1990s - Present): Prevented speeding and unauthorised train movements by enforcing safety parameters.
- Communications-Based Train Control (CBTC) (2000s - Present): Used radio signals to continuously monitor train positions, enabling moving block operation (trains running closer together safely).
- Positive Train Control (PTC) (2000s - Present, USA): Enforced speed restrictions and prevented signal violations via digital monitoring.
Railway signalling has now entered the fully digital, AI-driven era, integrating real-time data, automation, and predictive analytics. The Cutting-Edge Technologies used include:
- ERTMS (European Rail Traffic Management System) & ETCS (European Train Control System): Standardised digital signalling across Europe, allowing interoperability between countries. Level 2 and Level 3 use wireless communication to replace physical signals.
- AI & Predictive Analytics: Uses big data and machine learning to predict track failures and optimise train scheduling.
- Digital Twin Technology: Creates virtual simulations of railway networks to test and optimise signalling systems before deployment.
- 5G & IoT-based Signalling: Enables real-time data exchange between trains and control centers, improving efficiency and response time.
Modern railway signalling technologies
The concept of automatic train control (ATC) emerged in the early 1900s, when the Great Western Railway in the UK implemented an early system in 1906. When first launched, the ATC in general, and its later derivative systems like Automatic Train Protection (ATP) and Automatic Train Operation (ATO), significantly enhanced railway safety and efficiency by preventing accidents caused by human error and optimising train operations. These were followed by the development of more advanced systems like the Automatic Train Stop (ATS) in the 1920s and 30s.
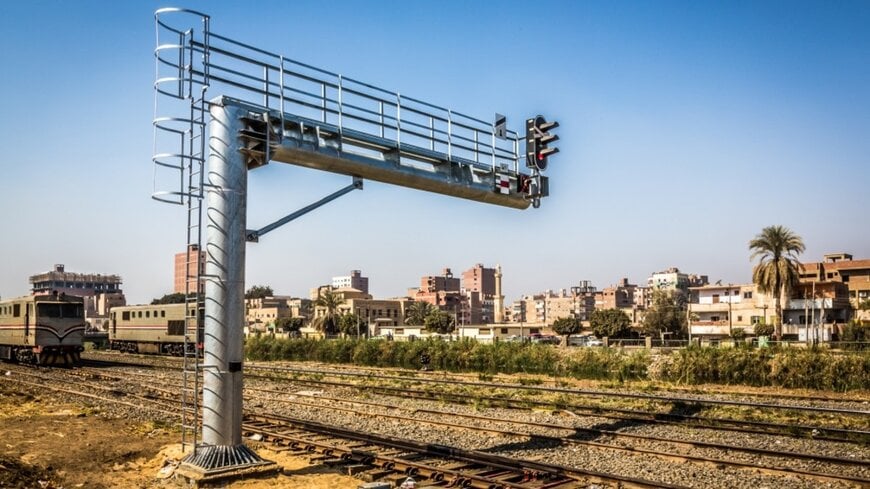
Computer-based interlocking signalling system Smartlock 400. Photo credit: Alstom
The basic purpose of ATC, which was an advanced railway signalling system of that era, was to automate train operations to improve safety, efficiency, and reliability. ATC consisted of three key subsystems:
- Automatic Train Protection (ATP) – Ensured trains operated within safe speed limits, which prevented collisions by enforcing speed restrictions, stopping trains if necessary.
- Automatic Train Operation (ATO) – Automated train acceleration, deceleration, and station stopping for smooth operation, though human oversight was still required in many systems.
- Automatic Train Supervision (ATS) – Managed train schedules, optimised train flow, and adjusted operations in real-time based on demand and disturbances.
- Optimised train spacing, ensuring trains maintain safe headways (the distance between trains), reducing congestion and minimising delays.
- Precise speed control by adjusting train speeds dynamically based on track conditions, reducing sudden braking and improving ride comfort.
- Efficient train scheduling with coordinated train movements in real-time to maximise throughput and minimise waiting times.
- Reduced human error, as automation minimised the risk of accidents due to operator fatigue or mistakes.
- Improved energy efficiency with smooth acceleration and braking patterns thereby reducing energy consumption.
- Better response to disruptions with real-time monitoring that allowed quick rerouting and adjustments in case of delays or breakdowns.
Key features of CBTC:
- Continuous train location tracking – Unlike conventional track circuit-based systems, CBTC uses onboard sensors (like transponders or odometry) and radio communication for real-time train positioning.
- Flexible headways – Can reduce the gap between trains, allowing higher frequency service without compromising safety.
- Driverless operation – Enables fully automated (Grade of Automation 4 - GoA4) driverless train operation, reducing operational costs and human errors.
- Precise speed and stopping control – Ensures smooth acceleration, deceleration, and precise station stopping, improving passenger comfort.
- Dynamic headway adjustment: Allows trains to run closer together, increasing network capacity.
- Real-time traffic management: Adapts to disruptions, optimising train movements dynamically.
- Seamless integration with urban transport: Works well in congested metro systems where high efficiency is required.
Key features of ETCS:
- Multiple levels of automation: Level 1 – Fixed block-based system with intermittent data updates via balises (trackside beacons); Level 2 – Continuous communication via GSM-R, allowing higher speeds and reduced signal dependency; and Level 3 – Full train-to-train communication, removing fixed blocks and maximising track capacity (still under development).
- Interoperability across countries: ETCS standardises signalling across Europe, allowing seamless train travel between nations.
- Enhanced safety: Prevents speeding, enforces braking curves, and ensures compliance with route permissions.
- Supports high-speed rail: Enables safe operation of high-speed trains (>300 km/h).
- Reduces signal reliance: Digital communication allows smoother train operations without needing fixed signals.
- Optimises train speeds & spacing: ETCS adjusts train speeds dynamically to prevent bottlenecks.
- Increases track capacity: ETCS Level 3 (future implementation) will eliminate fixed blocks, allowing more trains on the same track.
Key components of advanced railway signalling systems
Regardless of the individual systems used by different operators, advanced railway signalling systems operate with the help of certain key components. These include:
- Centralised traffic control (CTC) – A centralised system that monitors and manages train movements across a railway network. Operators can control signals and track switches remotely to optimise traffic flow.
- Interlocking systems – Interlocking systems are essential in railway signalling to prevent conflicting train movements through junctions, switches, and crossings. They ensure that signals, track switches (points), and level crossings operate in a coordinated and safe manner by preventing conflicting movements. There are different types of interlocking systems ranging from the early systems like Mechanical interlocking; later improvements such as Relay-based or Electromechanical interlocking; or the latest Electronic Interlocking (EI) or Computer-Based Interlocking (CBI) systems.
- Train detection systems – These ensure track occupancy monitoring to prevent accidents. Key technologies for train detection include: i) Track circuits – Detecting presence of trains using electrical circuits; ii) Axle counters – Counting wheelsets to confirm train location; and iii) Radar & LiDAR sensors – Used in modern, high-tech railway applications.
- Positive Train Control (PTC) – This is a US-based safety system designed to prevent train collisions, derailments, and speed violations. It uses GPS, trackside sensors, and onboard computers for real-time monitoring.
- Trackside signalling equipment – Includes traditional colour light signals, LED signals, and mechanical semaphore signals; also balises (transponders) and beacons for communication with onboard systems.
- Wayside & onboard communication systems – These use GSM-R (Global System for Mobile Communications – Railway), LTE-R, and future 5G networks. They enable real-time communication between trains and control centres.
- SCADA (Supervisory Control and Data Acquisition) – for monitoring and control of power supply, signalling, and infrastructure remotely. This provides real-time diagnostics to prevent failures.
- Cybersecurity & data analytics – Modern signalling systems integrate AI-driven analytics for predictive maintenance. Cybersecurity measures are implemented to protect against hacking and system failures.
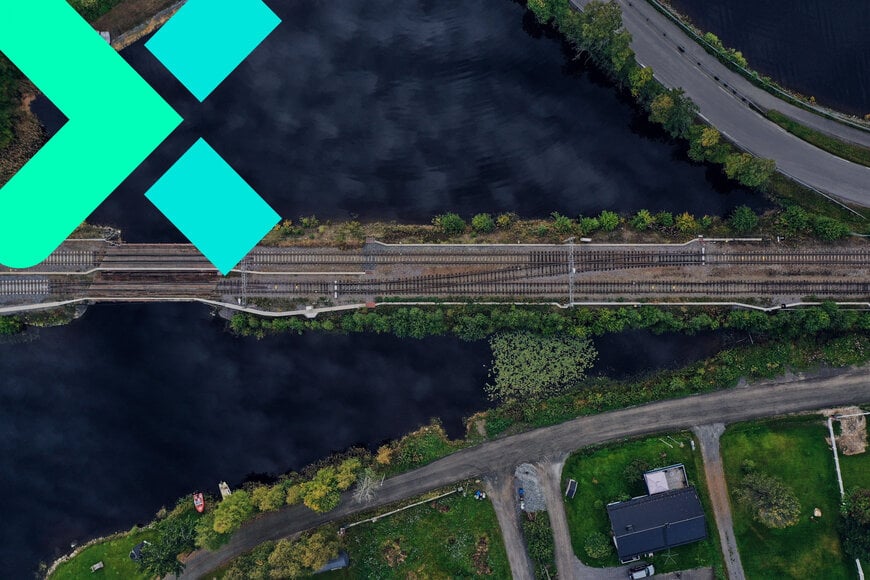
Signaling X – rail signaling and control systems into the digital future. Photo source: Siemens Mobility
Benefits of advanced railway signalling and control systems
When it comes to a mass transport system like the railways that carry millions of passengers worldwide every single hour, safety is of paramount importance. Advanced railway signalling and control systems are crucial for ensuring safe, efficient, and reliable train operations by preventing collisions, regulating speeds, and optimising traffic flow through automated signals and communication technologies. Enumerated below are some of the key benefits of signalling and control systems in railway networks:
i. Enhanced Safety
- Collision prevention: Automatic Train Protection (ATP) and Positive Train Control (PTC) systems prevent collisions by enforcing speed limits and stopping trains if necessary.
- Reduced human error: Advanced signalling minimises the risks associated with driver fatigue or misjudgment.
- Real-time monitoring: Centralised control systems provide continuous monitoring, allowing immediate response to potential hazards.
- Optimised train spacing: Systems like Communication-Based Train Control (CBTC) and European Train Control System (ETCS) allow for shorter headways between trains, increasing line capacity.
- Higher frequency of services: More efficient use of track infrastructure enables increased service frequency without additional tracks.
- Automated Train Operations (ATO): Reduces delays by ensuring precise acceleration, braking, and stopping.
- Energy efficiency: Smart control systems optimise speed profiles and braking to reduce energy consumption.
- Predictive maintenance: Condition-based monitoring detects potential failures before they cause disruptions.
- Reduced delays: Efficient train scheduling and real-time adjustments help minimise service disruptions.
- Better information systems: Real-time train tracking and automated announcements improve passenger communication.
- Standardisation across networks: Systems like ETCS and CBTC enable cross-border train operations, supporting international rail travel.
- Integration with other transport modes: Smart signalling can coordinate rail services with buses, metros, and trams for smooth multimodal travel.
- Lower maintenance costs: Digital signalling reduces the need for physical trackside equipment, cutting maintenance expenses.
- Optimised workforce deployment: Automation reduces dependence on manual intervention, streamlining operations.
Challenges in implementing advanced signalling systems
The tools of technology are available for the railway signalling systems as they are for other aspects of modern living. Yet, implementing advanced signalling systems in digital railway networks presents several challenges across multiple dimensions. The following paragraphs present an overview of some of these challenges in terms of implementation and maintenance costs, infrastructure upgrades, software integration, cybersecurity risks, and interoperability/standardisation issues.
i. Challenges in implementation and maintenance costs
- High initial investment: Advanced signalling systems such as ETCS and CBTC require substantial financial investment in hardware, software, and operational modifications.
- Cost of retrofitting existing systems: Older railway networks require extensive modifications, including upgrading legacy signalling infrastructure, which can be expensive and time-consuming.
- Ongoing maintenance expenses: Modern digital signalling relies on continuous software updates, sensor recalibration, and system diagnostics, increasing lifecycle costs.
- Return on investment (RoI) considerations: Operators may struggle to justify the high upfront costs, especially in regions with lower railway traffic density or limited government funding.
- Compatibility with legacy systems: Many rail networks still rely on traditional relay-based or analog signalling, making digital integration complex and costly.
- Need for high-quality communication networks: Advanced signalling depends on robust, low-latency communication networks (e.g., 4G/5G, fiber optics). Ensuring uninterrupted connectivity across vast railway networks is a challenge.
- Power supply and redundancy: Many railway lines require enhanced power distribution systems to support new signalling technologies, adding to infrastructure costs.
- Trackside equipment modernisation: Deployment of sensors, beacons, and transponders along tracks is necessary for digital systems, which can be logistically challenging in remote areas.
- Integration with existing train control systems: Different railway operators use varied legacy software, requiring complex and costly integration with modern signalling solutions.
- Real-time data processing & synchronisation: Digital signalling depends on real-time data exchange between trains, control centers, and trackside equipment. Ensuring data consistency is critical but technically complex.
- Software bugs and system failures: Any glitches in automated signalling software can lead to service disruptions, posing operational and safety risks.
- AI & predictive maintenance complexity: While AI-driven predictive maintenance can improve efficiency, implementing and training such systems requires significant expertise and investment.
- Increased vulnerability to cyberattacks: As railways become more digitised, they become attractive targets for cybercriminals, including ransomware, data breaches, and system sabotage.
- Lack of cybersecurity awareness and standards: Many railway operators still lack comprehensive cybersecurity strategies, making systems vulnerable to attacks.
- Third-party risks: Signalling systems often rely on software and hardware from multiple vendors, increasing the risk of supply chain vulnerabilities.
- Potential safety risks: A cyberattack could disrupt signalling, potentially leading to train collisions or derailments.
- Challenges in incident response: Coordinated incident response across multiple stakeholders (railway operators, government agencies, cybersecurity teams) is difficult due to jurisdictional and technical barriers.
- Diverse signalling systems across countries & operators: Rail networks worldwide use different signalling protocols, such as ETCS in Europe, CBTC in metros, and PTC in the US, leading to interoperability issues.
- Lack of unified standards for digital signalling: While global initiatives (e.g., ERTMS for high-speed rail) aim to standardise systems, regional variations still exist.
- Cross-border operations complexity: Trains traveling across international borders must switch between different signalling systems, requiring costly multi-system onboard equipment.
- Vendor lock-in risks: Some operators depend on proprietary signalling solutions from specific vendors, making future upgrades and integrations difficult.
- Harmonisation challenges: Aligning multiple national and regional railway authorities under a single digital signalling standard remains a significant hurdle.
- Global standardisation initiatives (e.g., full-scale adoption of ERTMS/ETCS Level 3 to unify signalling across regions).
- Mandating open-source or interoperable systems to prevent vendor lock-in.
- Collaboration between railway authorities and technology providers to ensure smoother transition strategies for legacy systems.
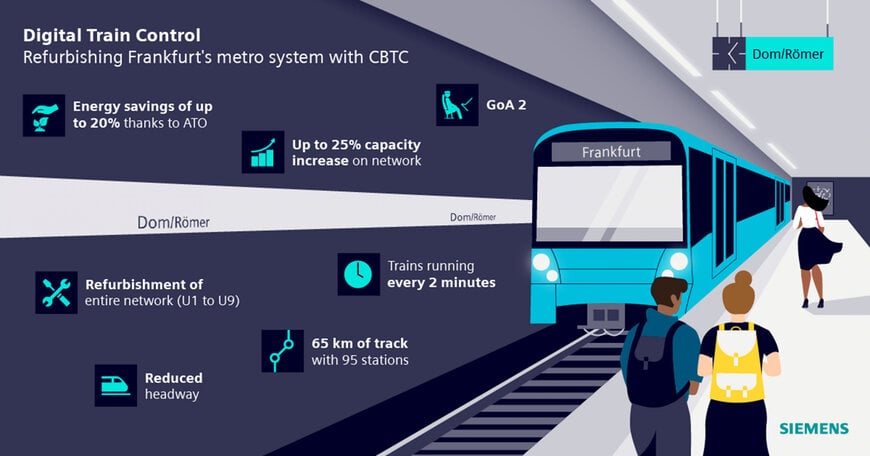
Digital train control system for the Frankfurt metro. Photo Credit: Siemens
Future trends and innovations in railway signalling
In a world of rapidly evolving technologies, no solution is permanent as there is always room for improvement. The current generation of railway signalling and control systems are quite advanced and sophisticated, but still there are shortcomings that become obvious when incidents occur, some leading to loss of lives. On January 5, 2024, two trains collided near Cicalengka Station in Bandung Regency, Indonesia, resulting in four fatalities and 42 injuries. The collision was attributed to an uncommanded signal leading to a false clear, caused by aging hardware in the signalling system. In June 2024, a collision occurred in the State of West Bengal in India involving a passenger train, the Kanchanjunga Express, and a freight train. The freight train reportedly ignored multiple red signals, leading to the crash. However, some sources suggest that a faulty automatic signal, defective since early morning, may have contributed to the incident. More recently, in early March 2025, services between London Paddington and Reading, as well as Heathrow Airport, were suspended due to a signalling fault, causing much chaos and delays in services during peak hours.
So what exactly are the future trends and innovations for a foolproof railway signalling system? Once again, new and emerging technologies offer some effective solutions in this context, which are summarised below.
Artificial Intelligence and Machine Learning (AI and ML) could offer some solutions based on:
- Predictive maintenance: AI-driven analytics can predict failures in signalling equipment, reducing downtime and enhancing safety.
- Automated Train Operation (ATO): AI optimises train movements, ensuring smooth acceleration, braking, and scheduling.
- Real-time anomaly detection: Machine learning models analyse vast amounts of signalling data to detect faults and optimise routes dynamically.
- GNSS-based signalling: GPS and Galileo enhance train positioning, reducing reliance on trackside equipment and enabling cost-effective operations.
- ERTMS evolution: satellite technology improves the European Rail Traffic Management System (ERTMS), enhancing train tracking and control.
- Remote monitoring & operations: satellite-based systems enable real-time monitoring of remote railway sections, improving safety and efficiency.
- Ultra-low latency communication: 5G enhances real-time train-to-ground communication for faster and more reliable signalling.
- Edge AI for decentralised control: Edge computing processes signalling data closer to the source, reducing delays and improving decision-making.
- Enhanced passenger safety & experience: 5G enables high-speed connectivity for surveillance, infotainment, and smart train operations.
In conclusion, advanced railway signalling and control systems are revolutionising the global rail industry by enhancing safety, optimising efficiency, and increasing network capacity. The adoption of technologies such as the European Train Control System (ETCS), Positive Train Control (PTC), and Communication-Based Train Control (CBTC) is enabling more precise and automated operations, reducing human error, and ensuring seamless interoperability. As rail networks continue to modernise, integrating AI, IoT, and digital twin technologies will further transform railway operations, making them smarter, more sustainable, and resilient to future demands. The future of railway signalling lies in continued innovation, collaboration, and investment in cutting-edge solutions that will drive the industry toward a more connected and intelligent transportation ecosystem.
References
1. https://www.globalrailwayreview.com/core_topic/signalling-control-communications/
2. https://www.softechrail.com/advanced-signalling-train-control/
3. https://www.questglobal.com/insights/thought-leadership/future-of-signaling-embracing-innovation-for-safer-smarter-railways