Keeping Rail 4.0 connected
PEI-Genesis highlights the role of connectors in enabling autonomous and intelligent rail systems.
www.peigenesis.com
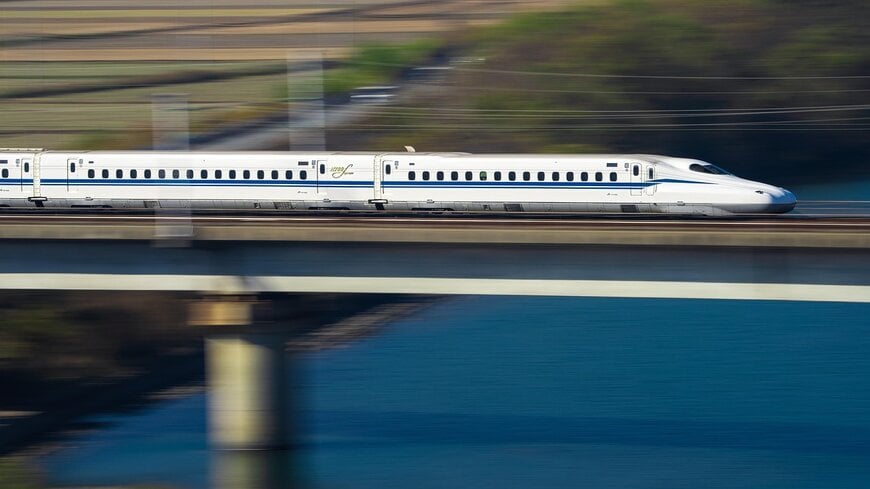
Rail operators are making significant investments in digitalisation and automation, worldwide. In Germany, Deutsche Bahn is trialling fully automated trains in Hamburg as part of its ‘Digital Rail Germany’ initiative, aiming to increase capacity and reduce emissions without expanding physical infrastructure. Meanwhile, East Japan Railway Company (JR East) is advancing plans to introduce driverless Shinkansen bullet trains by the mid-2030s.
Together, these efforts signal a wider shift towards rail systems built around AI, real-time analytics and high-speed communication, all of which depend on reliable interconnect technology.
Connecting complexity
The railway environment poses some of the most severe conditions for electrical interconnects. Rolling stock and trackside hardware are exposed to constant vibration, harsh temperature extremes from -55°C up to +200°C as well as high humidity. Similarly, connectors need to be immune to exposure to contaminants such as dust, oil and de-icing agents.
In addition, electromagnetic interference (EMI) generated by traction drives and overhead cables can jeopardise signal integrity unless connectors are effectively shielded.
Connectors designed for rail applications must be ruggedised to meet stringent international standards such as EN 50155 and EN 45545-2, NFPA 130, VG 95234 and MIL-DTL-5015. These benchmarks define the connector’s ability to withstand shock, vibration, fire exposure and long-term environmental stress. RoHS and REACH variations along with corrosion resistant platings, make for rugged and reliable interconnect solutions in the harshest environments.
When it comes to autonomous trains, the demands on connectors increase further. They must be capable of supporting high-speed data transmission protocols such as Gigabit and 10-Gigabit Ethernet (typically Cat 6A and Cat 7), USB 3.1 and fibre optic interfaces.
These protocols are essential for handling real-time data streams from sensors, LiDAR systems, onboard diagnostics and communication networks. Data rates in these environments can exceed 10 Gbps, especially when multiple high-bandwidth systems, such as video surveillance, telemetry and predictive maintenance sensors are operating concurrently.
Mechanical resilience remains critical. Connectors generally incorporate bayonet or threaded coupling systems to maintain secure connections under vibration. Contact retention mechanisms are designed for longevity, often rated for thousands of mating cycles. Contacts are generally gold-plated to minimise corrosion and offer low contact resistance for a prolonged time. These are also available in silver-plated versions.
Ease of maintenance is another crucial factor, particularly for retrofit applications. Modular connector designs and coding schemes enable simple installation and error-proofing. In addition, quick-disconnect configurations ensure quick field servicing with minimal downtime.
Future-proofing rail connectivity
As Rail 4.0 evolves, so too must the technology that supports it. Upcoming innovations in train autonomy and electrification demand connectors with greater bandwidth, higher power ratings and smarter integration capabilities.
For example, the development of distributed traction systems and battery-electric multiple units (BEMUs) introduces new requirements for high-voltage, high-current connectors that can handle regenerative braking energy and rapid charging. These connectors must include safety interlocks, arc suppression features and compliance with standards such as IEC 61373 for shock and vibration.
Simultaneously, increased deployment of real-time diagnostics and condition monitoring means that connectors must support multiple sensor interfaces. Emerging designs now incorporate built-in diagnostics, enabling connectors themselves to report on temperature, contact resistance, or mechanical wear, turning passive components into intelligent assets.
Modularity is another key trend. Future rail systems will demand flexible, reconfigurable architectures to accommodate upgrades and regional customisations. Connectors that support daisy-chaining, backplane mounting and tool-less assembly are increasingly favoured to reduce downtime and simplify system expansion.
PEI-Genesis supplies a wide range of connectors engineered specifically for challenging rail environments. Our portfolio includes high-power solutions designed to handle demanding electrical loads, as well as high-speed data connectors used in communications and control systems. These connectors are designed to meet strict global rail standards, including EN 50155. With modularity and rugged design as core principles, our connectors support applications ranging from onboard control systems to trackside signal units, playing an essential role in powering the next generation of autonomous rail technology.
As the global rail industry accelerates towards full automation, the supporting technologies behind the scenes are just as vital as the software that guides the trains. Connectors play a crucial role in delivering the reliability, safety and performance required by Rail 4.0. They serve as the nervous system of modern trains, making real-time communication and electrified propulsion possible in even the harshest environments. Looking ahead, the connector landscape will continue to evolve alongside rail innovation, offering smarter, faster and more resilient solutions that keep the railways of the future on track.
www.peigenesis.com